Products
- Circular Connectors & Cable Assemblies
- D-Sub Connectors
- IP67 D-Sub Connectors
- D-Sub Backshells
- Micro-D Connectors & Cable Assemblies
- Power-D & Combo Mixed Connectors
- Push Pull Connectors
- D-Sub & Micro D Hardware
- Modular RJ45 Connectors
- USB Connectors
- D-Sub Adapters & Gender Changers
- SCSI .085"/.050"
- .050 Ribbon
- Headers & Receptacles
- Bayonet Connectors
High Data Rate Connectors for Telematics Systems
Telematics systems are one example of a rugged system that requires significant data processing and transmission capabilities.
Telematics tend to use a specific set of connectors, depending on the environment where the system will be deployed, and these connectors will have standardized construction and pin arrangement to enable interoperability.
To ensure newer vehicles can collect and process massive amounts of data from sensor suites and a vehicle’s electric control units (ECUs), these systems need to implement high data rate connectors that can enable the required bandwidth for proper operation. Bandwidth is an important requirement to ensure data streams are properly collected and processed, but rugged construction is another major requirement that ensures telematics system performance. In this guide, we’ll examine some of the operational requirements of telematics systems and how high data rate connectors play a role in ensuring operational effectiveness.
Compute Requirements in Telematics Systems
As automobiles have become more advanced, with more ECUs and sensing systems being integrated into vehicles, the compute requirements have continued to increase. Telematics systems are responsible for collecting and aggregating data from multiple ECUs placed around the vehicle, which requires serial transmission over multiple protocols operating at high data rates. Connecting multiple assemblies at high data rates requires a terminated connector and cable assembly that can provide the required bandwidth for serial data transmission at high bit rates.
Connectors and cable assemblies for automotive telematics modules currently accept power and data as standardized under several protocols:
- Power with wide input voltage (as large as 48 V)
- Data transfer between ECUs over CAN FD or SAE standardized protocols (J1939, J1587, and/or J1708)
- 802.11 wireless protocols, which may include communication between an electric vehicle’s wireless BMS and a telematics unit
- GPS/GNSS navigation data
- Automotive Ethernet
- Onboard diagnostics (OBDII) interface
Data being transferred via any of these protocols could first be aggregated in an ECU and sent over a serial connection, or it could be collected directly into a telematics system in parallel. Automotive Ethernet is the newest in-vehicle networking technology being used to provide high data transfer rates between sensors and ECUs/telematics systems, although these will not use the standard CAT 5 cable assembly and connector. Newer EVs are using a wireless BMS to monitor battery health and reduce total vehicle weight, so it may be beneficial for an ECU or telematics unit to support one or more 802.11 protocols to collect battery data.
Since telematics systems need to be compact to support all these features, connectors for an external cable assembly or wiring harness should take up a minimal amount of real estate. Multiple connectors may be needed to support all these data streams into the device. The connectors used in telematics units (except for the onboard diagnostics interface connector) are not standardized. This gives systems designers some freedom to choose a telematics connector that will work best for their systems as long as the connectors can withstand environmental stresses.
High Data Rate Connector Options for Telematics
There are other environmental challenges to be considered when designing telematics systems and selecting connectors. The interior of a vehicle presents several hazards that can reduce the reliability of electronic equipment, including telematics units and ECUs. Some of the operating hazards seen by a telematics system include:
- Strong low-frequency vibrations
- High temperatures
- Mechanical forces or impacts
- ESD during exposure to high voltages
- Exposure to solid debris or moisture
Connectors for telematics units need to be rugged enough to withstand these challenges while also enabling high data transfer rates required in modern automobiles. Today, there are many ruggedized versions of standard high data rate connectors that are available for telematics systems.
Circular Connectors and Push-Pull
Circular M5/M8/M12 cables can interface directly with sensors or ECUs while providing high mechanical strength and reliability. The screw retention mechanism provides the highest mechanical strength and reliability. They can also support high data rate protocols like Ethernet operating at 100 Mbps or higher data rates.
VULCON connectors provide flexible conductor counts that can support data transfer up to 10 Gbps.
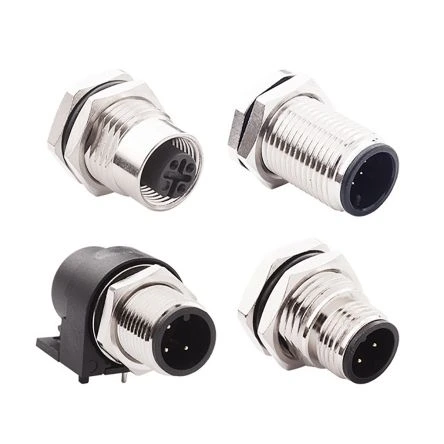
Push-pull connectors offer additional reliability as they include a latching mechanism to help secure the cable assembly to its receptacle. An accidental disconnect is difficult as the connector body needs to be squeezed to release the cable. These connectors can also provide high data rates used in serial protocols, as well as high power ratings to support multiple features in a telematics system.
D-sub Connectors
A D-sub connector assembly can be used with a standard or custom pinout that aggregates multiple data streams and power into a single connector. Higher pin count D-sub connector assemblies are normally used to carry data over parallel interfaces or multiple serial interfaces like CAN-BUS. With a simple modification of the pinout, it’s possible to consolidate moderate power inputs and a serial data stream into a single connector with low profile. For high power needs, Norcomp offers the Power-D connector, available with 20 or 40 amp power contacts. All D-sub connector receptacles/headers can be board-mounted or panel/chassis mounted.
D-sub connectors are available with coaxial connections that can provide very high data transfer rates in a rugged assembly.
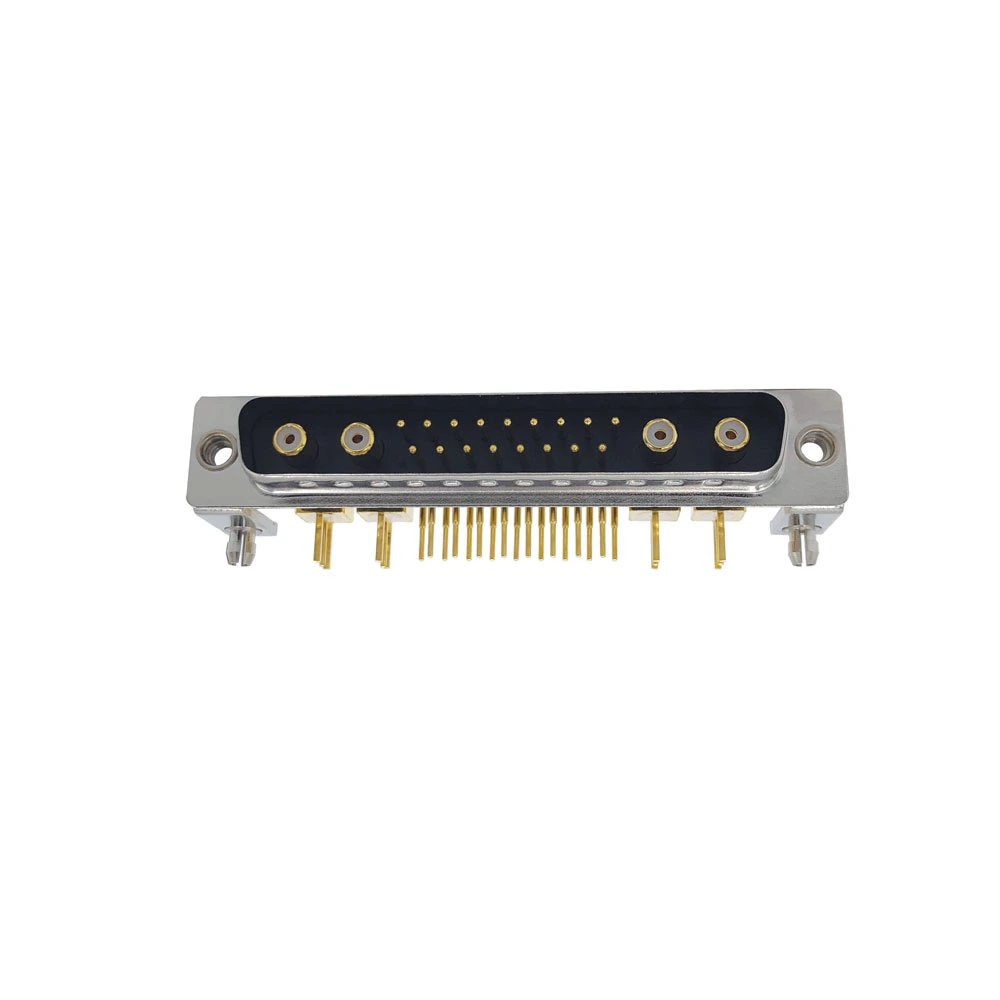
These rugged connector options offer a lot of flexibility in terms of conductor count, form factor, retentio/keying mechanism, and power ratings. Versions of these standard connectors that meet IP67/IP68 ratings are also available. Stainless steel or housings are also available for these connectors when higher levels of reliability are required. When one of these standard connector options does not meet conductor count, data rate, or power requirements, it’s worth considering a custom connector design that can meet these requirements.
When you need to find standard or custom connector assemblies for telematics systems in advanced automobiles, Norcomp provides interconnect solutions that are designed for maximum reliability in harsh environments. Norcomp’s product lines are Rugged Environment Certified (REC) and are ideal for use in automotive telematics, robotics, industrial equipment, and other demanding applications. Custom connector options can be built to IP66 or IP67 ratings to ensure maximum reliability. Contact Norcomp today to learn more about our standard or custom interconnect solutions.
Go Back