Table of Contents
- CONNECTOR TECHNOLOGY
- WHAT ARE THE DIFFERENT TYPES OF CONNECTORS?
- CONNECTOR APPLICATIONS
- CONNECTORS FOR COMMUNICATIONS APPLICATIONS
- CONNECTORS FOR INDUSTRIAL APPLICATIONS
- CONNECTORS FOR MEDICAL APPLICATIONS
- CONNECTORS FOR MILITARY APPLICATIONS
- CONNECTORS FOR ROBOTICS APPLICATIONS
- RUGGED ENVIRONMENT CERTIFIED CONNECTORS
- CONNECTORS FOR TELEMATICS APPLICATIONS
- CONNECTORS FOR TEST AND MEASUREMENT
- CONNECTORS FOR TRANSPORTATION APPLICATIONS
- RESOURCES
Connectors play a key role routing signals and power between electronic systems in almost all fields: industrial machines, aircraft, medical equipment, robotics, communications, test & measurement, and many others.
Within an electronic system, internal connectors join up printed circuit boards (PCBs) and modules allowing these devices to be manufactured and tested separately before final assembly, saving manufacturing cost and time.
Many connectors also act as the interface between equipment and the outside world and protect sensitive internal electronics. In this case, the connector not only facilitates reliable transfer of signals and power, but also must withstand external conditions and maintain the integrity of the case design.
CONNECTOR TECHNOLOGY
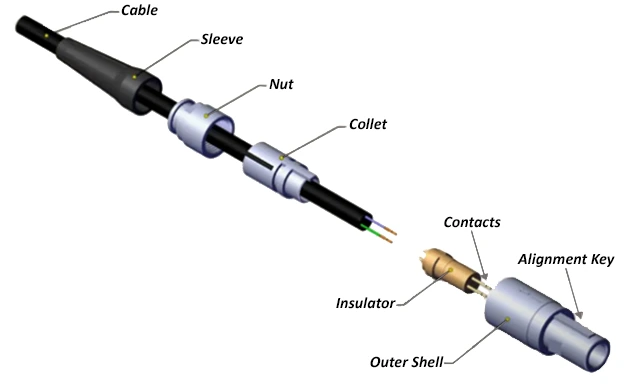
A connector consists of an outer shell (housing) that protects the internal elements; an internal insulator that holds multiple pins or sockets in a rigid structure to preventing them from touching; and a means of securing the connector to the mating receptacle. Figure 1 shows the construction of a push-pull circular connector. This connector shell includes a key to ensure that the connector and receptacle are properly aligned.
Each element of a connector is typically available in a choice of materials to suit different applications.
CONTACT TYPE
Connector contacts can be manufactured in several ways. Stamped and formed contacts are designed for use where wire termination costs are of primary concern while maintaining reliable performance. They can also be fed into automated crimping machines, making them more suited to high-volume production.
Machined contacts are higher cost, but offer greater power density, lower contact resistance, and higher current than stamped contacts, and provide better strength and durability.
CONTACT TERMINATIONS
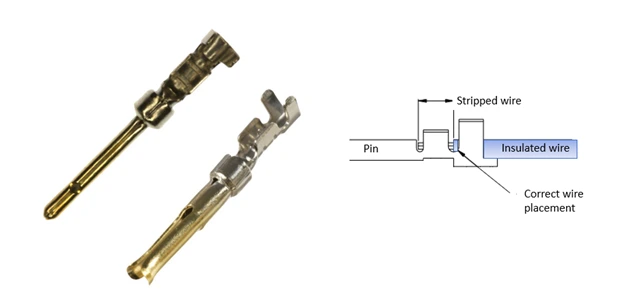
The termination type refers to the method for connecting the individual connector contacts to a mating cable or PCB. There are three main types of contact terminations:
- In a crimp termination (figure 2) , the contact is mechanically tightened (crimped) around the wire to make electrical contact. Another part of the contact is crimped around the wire insulation. The crimp operation takes place before each contact with its wire attached is inserted into the connector housing. A crimping tool is used to apply pressure and compress the contact section tightly around the wire and the insulation.
- In a solder termination, each connector pin includes a solder cup or pin on the end to which a wire is soldered. Alternatively, the pins are inserted through holes in a PCB. Figure 3 shows the different options.
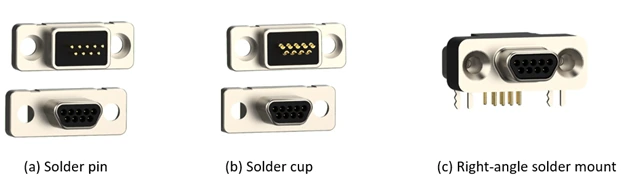
- Insulation displacement connectors (IDCs) are used to connect insulated wire or cable to a device without pre-stripping the cable or wire. By incorporating a sharp blade or multiple blades in the connector (figure 4), the insulation is cut as it is inserted. A ribbon cable is suitable for an IDC termination.
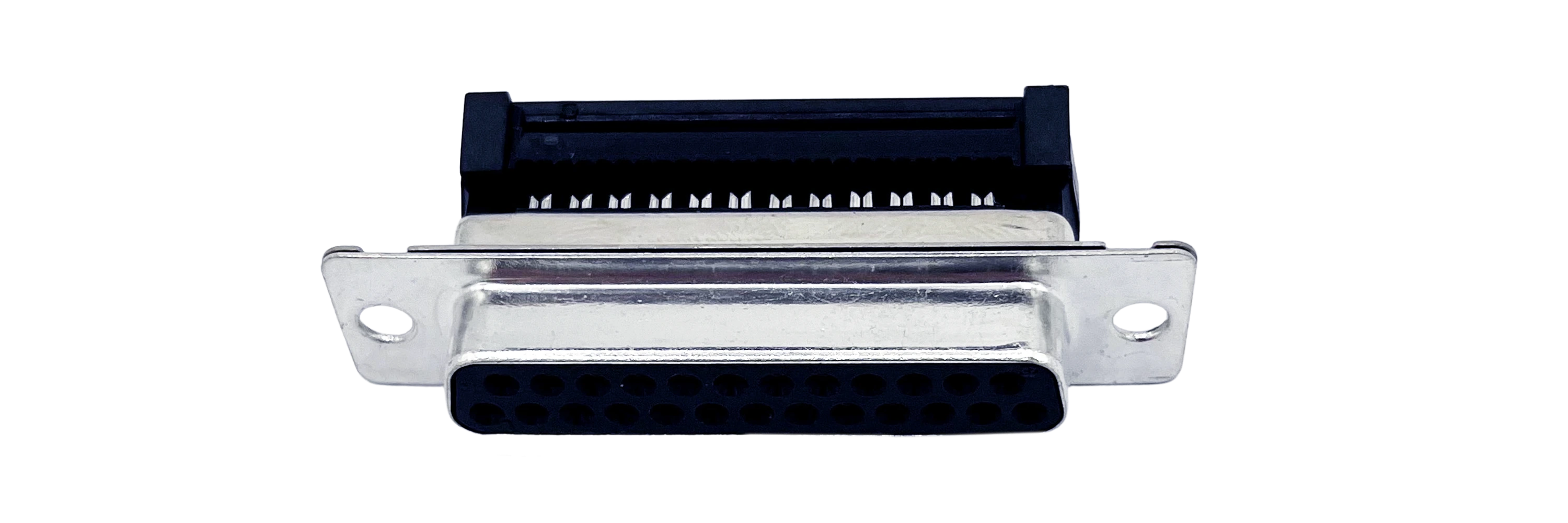
- Connectors with screw terminations allow the wire to be inserted into a receptacle, then secured with a built-in screw as shown in figure 5. These terminations are not as compact as other types, but have the advantage that wire connections can be attached, removed, and changed in the field.
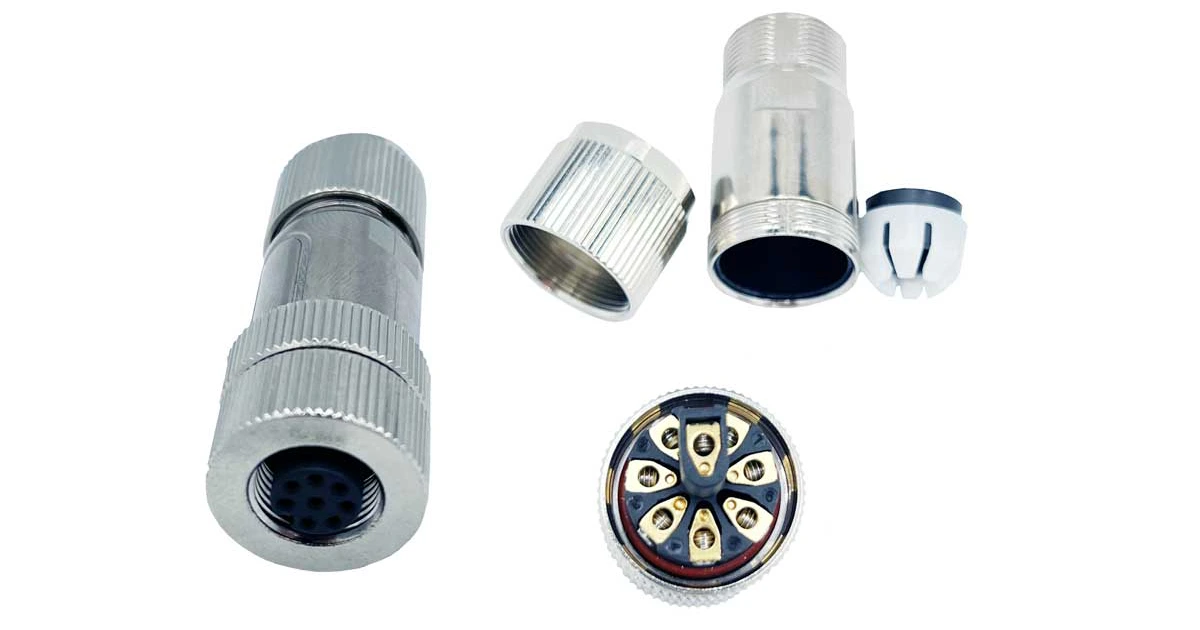
HOW TO FIND THE RIGHT CONNECTOR? KEY REQUIREMENTS & SPECIFICATIONS
Like any component, there is a set of key specifications associated with a connector. Physical size and shape are important factors. Some of the common types are industry-standard shapes, such as the “D” type, that are general-purpose in nature and used across multiple applications. Other connector types are associated with a particular application, such as the USB or SCSI connectors. Once the connector type has been selected, the designer must also specify a list of key requirements. Here are the main ones:
OPERATING TEMPERATURE RANGE
The operating temperature range of a connector is not critical for a commercial environment, but it is
an important consideration if the connector is to be used in harsh environments. The operating temperature range can vary widely depending on the application. Here are a few examples; consult the data sheet for specific ratings.
Connector type | Model Family | Temperature range |
circular connector | -40° to +85°C | |
flanged d-sub IP67 connector[BH2] | -25° to +85°C | |
push-pull connector, plastic shell | -20 ° to + 120 ° C | |
push-pull connector, metal shell | -40 C to +200 C | |
d-sub IP67 connector | -55 ° to + 125 °C |
Number of contacts
When choosing any connector type it is necessary to determine how many pins will be required. This may not only determine the actual connector part, but also the series of connector to be used. Depending on model, connectors may have from 2 up to 240 pin contacts.
NUMBER OF MATING CYCLES
All connectors undergo wear each time they are connected and disconnected. Often the life of a connector is specified in terms of the number of mating cycles, i.e. a connection and disconnection. Some connectors intended only to be disconnected for service and repair need a smaller number of mating cycles. Connectors for more general use must have a much larger number. This specification can affect the connector chosen for a particular application.
For sub-d and M-type connectors, the number of mating cycles is up to 750 depending on the type of contacts (machined or stamped and formed) and the gold plating thickness. Push-pull connectors are rated for 5000+ mating cycles. Go here to see the minimum cycle ratings.
CONNECTOR CONTACT SPECIFICATIONS
There are several specifications related to the connector contacts, including:
- Maximum wire gage
- Maximum current capability
- Contact resistance
- Maximum working voltage
The number of contacts in a given connector type can influence the contact specifications. A smaller number of contacts allows a larger contact size with greater current capability, lower contact resistance, and higher working voltage. The table below shows the contact specifications of two Quik-Loq™ 820B connectors with different numbers of contacts.
Connector P/N | # of contacts | Pin diameter (mm/”) | Max wire size (awg) | Max current (A) | Contact resistance (mΩ) | Working Voltage (V) |
820B002 | 2 | .9/.035 | 22 | 10 | 6 | 330 |
820B009 | 9 | .5/.020 | 28 | 2 | 10 | 200 |
INSERTION FORCE
When male and female contacts connect or disconnect, there is a level of friction between the pair of contacts. This provides a good electrical and mechanical connection and allows cleaning of the contacts. For a small number of contacts, this friction does not present a problem. D-Sub connectors, for example, have a maximum mating force of 3.3 newtons per contact and a minimum unmating force of 0.25 newtons per contact.
As the number of pins increases, though, so too does the force required to connect and disconnect the two connectors. This can be a problem for high pin-count connectors and may need to be considered[JH7] .
WHAT IS ZERO INSERTION FORCE?
For some specialist applications where very large numbers of pins are required, what are termed "Zero Insertion Force" (ZIF) connectors may be used.
When mating, the female connector does not allow the male pins to contact the female mating pins, considerably reducing the force. A lever on the side of the female connector brings them into contact once the two halves have mated. This reduces the insertion force to a very small value.
CONTACT (PIN) PITCH
Pitch refers to the distance between adjacent pins. The most common sizes are 1.27 mm (0.050”), 2.00 mm, and 2.54 mm (0.1”), although many other pitches are also used.
INGRESS PROTECTION (IP) RATING
The IP rating of a connector indicates the level of protection it provides against the incursion of solids, including dust, and liquids, including moisture or water. A connector’s IP rating is expressed in the form “IPXY”, where X and Y are numeric values.
The first digit in an IP rating indicates the level of ingress protection against solid objects ; from IP0x (no protection) to IP6x (complete protection against dust). The second digit refers to protection from liquids: from IPx0 (no protection) to IPx9 (protection against water jets). Ruggedized connectors meet a variety of IP standards: IP50, IP66, IP67, or IP68, depending on the application.
WHAT ARE THE DIFFERENT TYPES OF CONNECTORS?
There are numerous types of connectors optimized for different uses. Here are the main categories.
METRIC CIRCULAR CONNECTORS
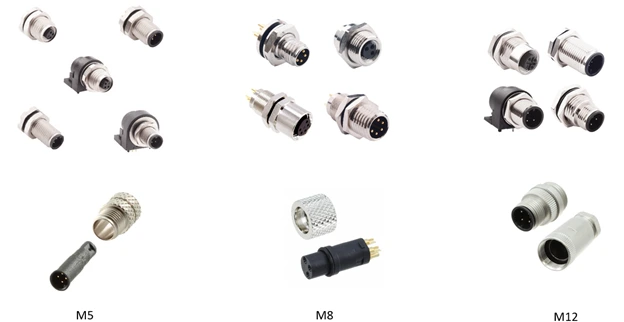
VULCON™ metric circular connectors (Figure 6) have screw threads and conform to the DIN EN 61076 standard. These connectors offer a robust waterproof cable-to-panel/PC board interface for demanding end-use applications. Contact-for-contact, these connectors take up less room than rectangular style connectors, enabling the efficient use of mounting connectivity space for multiple design-in applications. The flexibility of cabling options and various pin counts have made these circular connectors popular in manufacturing plants in multiple industries due to their rugged and reliable operation and suitability for numerous applications. The number after the M indicates size, from small to large.
M12 CIRCULAR CONNECTORS
The M12 circular connector was first utilized in the automotive manufacturing sector in the early 1980's. It has since become a leader in the industrial automation and industrial controls sector with its ability to endure stressful environments and protect against dust while remaining waterproof. M12 applications include industrial controls and automation such as remote process sensors, robotics control systems, ruggedized networking, & power conditioning systems.
M8 CIRCULAR CONNECTORS
The M8 circular connector quickly made its debut as a smaller more compact version of the M12. M8 connectors are used in applications requiring a rugged and robust fully shielded metal shell able to withstand shock and high vibration. M8 applications include medical devices, ruggedized data loggers & sensors, electronic gauges & metering, as well as avionics and marine electronics.
M5 CIRCULAR CONNECTORS
M5 connectors are ideal for many applications where a small yet rugged and compact connector solution is required to deliver a secure and reliable signal transfer. M5 connector applications include transportation and control systems, automated doors & ramps, sensor connectivity, as well as many data & communication device applications.
All metric circular connectors feature IP67/68 protection and are rated over the -40 °C to +85 °C temperature range. The table below shows the options available for each type.
Connector | Contact Count | Type | Shield |
M5 | 2,3,4 | cable mount, panel mount | Shielded, unshielded |
M8 | 3,4,5,6 | cable mount, panel mount | Shielded, unshielded, cable kit |
M12 | 3,4,5,6,8,12 | cable mount, panel mount, anti-vibration | Shielded, unshielded, cable kit |
PUSH-PULL CONNECTORS
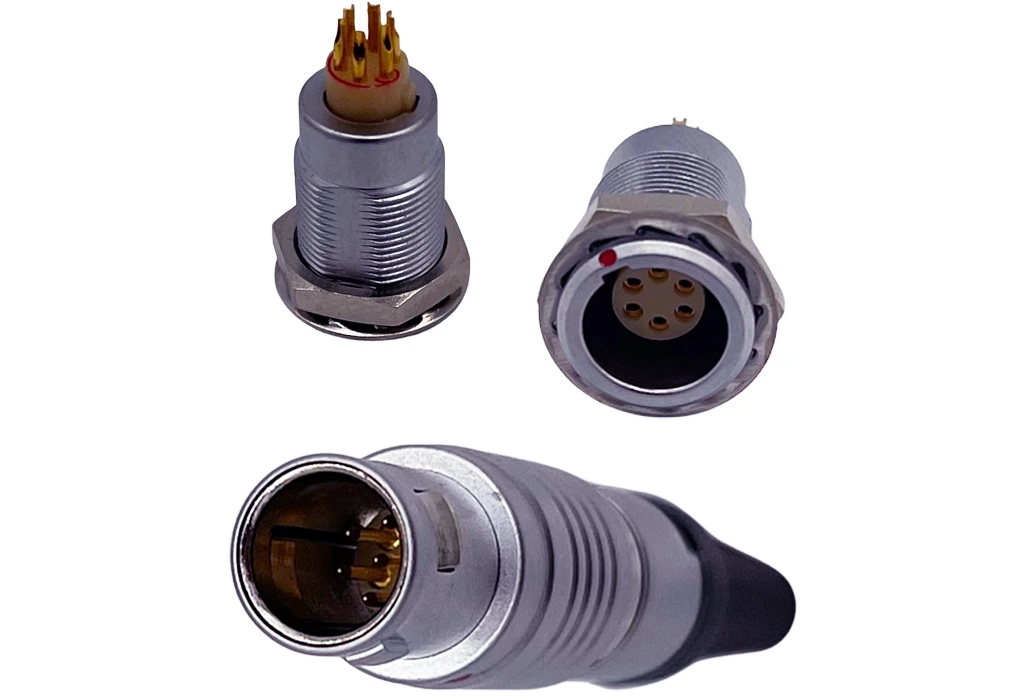
Circular push-pull connectors (figure 7) are ideal for applications that require quick connect and disconnect operation and high reliability. Examples can be found in test & measurement, instrumentation, medical equipment, and telecommunications.
Push-pull connectors are rated to REC (Rugged Environment Certified) standards. These connectors can withstand high levels of shock and high vibration found in harsh environments such as industrial automation, robotics, weather stations, and oil & gas installations.
QUIK-LOQ™ Circular Push-Pull Connector systems are rugged, sealed connectors ideal for high-reliability waterproof applications where quick connect / disconnect and environmental protection are required. There are several families of QUIK-LOQ™ connectors.
QUIK-LOQ™ features and benefits include:
- Rapid latching release mechanism with alignment key
- Small, rugged precision design
- Available in varying pin positions
- Accepts 14-28 awg wires (based on # of positions)
- Rated for 2 to 30 amps depending on # of positions
- High Mating Cycles (>5000)
- Machined contacts and housing
- 360° shielding for full EMI / RFI
METAL SHELL PUSH-PULL CONNECTORS
QUIK-LOQ Metal Shell Push-Pull Circular Connectors deliver a compact high-performance solution engineered to withstand shock and high vibration both indoors and outdoors in harsh environments.
IP50 Push Pull Connector Systems are ideal for instrumentation & medical markets where high mating cycles & quick connections are critical to performance. The rugged and precision-designed IP50 Push Pull Connectors are engineered with machined contacts and housing for optimal connectivity.
QUIK-LOQ™ IP67 Push Pull Connector Systems are rated for more than 5,000 mating cycles, designed with alignment key and rapid latching & release mechanisms. The series features 360° EMI/RFI shielding, and precision-machined contacts for the most reliable signal transfer in heavy-duty environments.
PLASTIC SHELL PUSH-PULL CONNECTORS
The QUIK-LOQ line of plastic push pull connectors are cost-effective solutions for applications requiring quick connect / disconnect in markets including medical devices, controls systems and test and measurement.
D-SUB CONNECTORS
The D-type connector has been used in many applications as a multi-way connector, and is well-known as the connector used for RS-232 serial links in desktop computers, although USB has now replaced it as the standard.
D-subminiature connectors, d-sub backshells, & hoods are still widely used for applications that require a rugged, robust I/O connector system. D-sub connectors are available in solder cup, solder pin, crimped, and IDC versions depending in model.
There are several families of D-sub connectors. Standard D-Sub connectors are available in sizes ranging from 9 pins to 50 pins. These are offered with nickel or tin shells with multiple different hardware options providing a flexible solution. High-density D-sub connectors offer 65% great pin density than the standard models and are available with 15 to 78 pins.
MICRO-D CONNECTORS
Machined MICRO-D connectors are less than one-third the size of standard d-subs and are designed for commercial applications where space is at a premium but a rugged I/O connector system is required. Examples include industrial robots, test & measurement, and hand-held & portable equipment.
There is a full range of MICRO-d connectors in 9-pin, 15-pin, and 25-pin configurations with both cable & board mount options. Features include a metal-to-metal interface for robust mechanical connections and shield effectiveness, a 2-amp contact rating, and operation over the -40°C To +125°C temperature range.
IP-RATED D-SUB CONNECTORS

Several options are available for applications that require D-Sub connectors with IP67-rated performance.
SEAL-D® IP67 rated waterproof d-sub connectors (figure 9) are sealed internally and maintain the same footprint as the standard d-sub product offering. This IP connector sealing technology has allowed many of our existing d-sub product offering to be manufactured in IP67 rated versions.
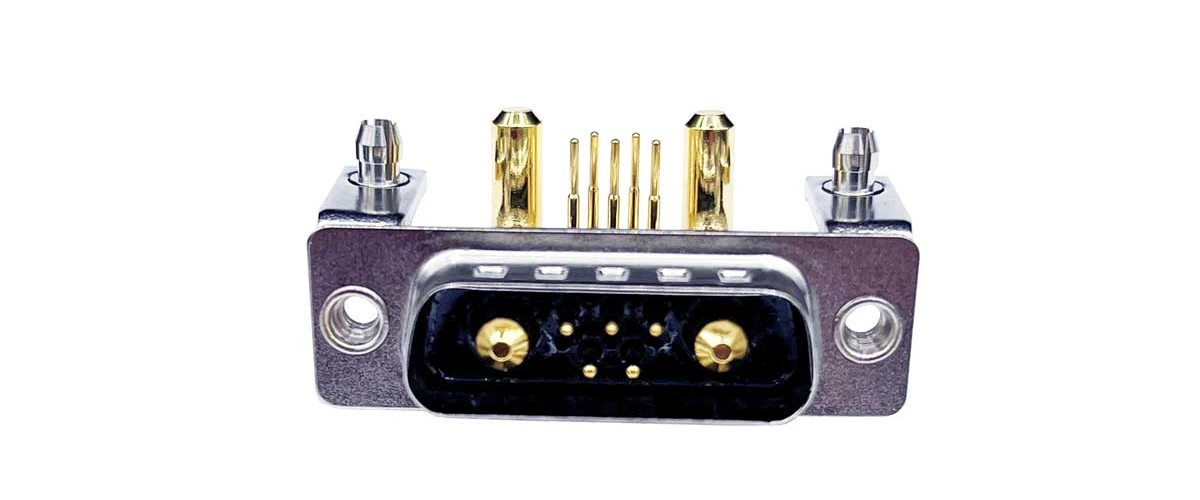
SEAL-D® connectors are designed for applications that require protection from heavy spray or are exposed to short-term submersion. Connectors are available in vertical and right-angle board mount types as well as solder cup for panel mount cable applications. Standard D-Subs are available in 9 pin, 15 pin, and 25 pin positions, and high density D-Subs are available in 15-pin, 26-pin, and 44-pin positions. Example applications include:
- Handheld computers, scanners, and printers that are used outdoors
- Remote sensors, gauges, and data loggers that are used outdoors
- Industrial and Medical equipment that is routinely subject to wash down
- Transmitters and emergency beacons that are subject to temporary submersion
- Gas, Electric, and Water metering systems that have embedded Smart Grid electronics
- Portable electric generation equipment (Gen Sets)
- Consumer and Commercial boating electronics (Radios, Scanners, Radar, DC Power Ports)
The SEAL-D® family are drop-in replacements for standard unsealed connectors; this eliminates the need to change PCB and sheet metal designs to upgrade to IP67 performance levels.
NANOOK flanged waterproof d-sub connectors offer a solution for a wide range of applications, including:
- Marine electronics (radios, scanners, radar, telematics)
- Industrial and medical equipment that is subject to washdown
- Remote sensors, gauges, and data loggers used outdoors
- Ruggedized laptops and printers
- Industrial robotics
Available in standard, high-density, and mixed layout configurations, these connectors are reliable, cost effective, and provide ease of installation.
D-SUB BACKSHELLS
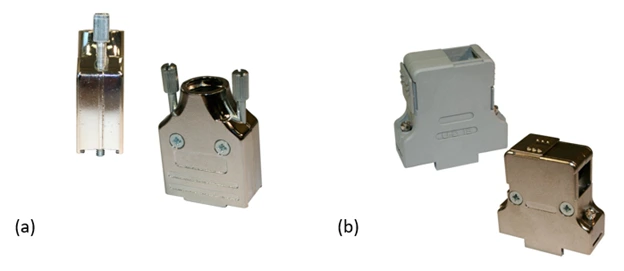
D-sub backshells are designed to maximize EMI/RFI shielding for optimal protection and performance. The comprehensive d-sub backshell product offering features a variety of options that improve the connection stability while maximizing cable strain relief in order to prevent damage to wires and contacts.
ARMOR D-Sub hoods are designed for rugged / robust applications including military, industrial, and aerospace. Featuring an all-metal hood die cast housing, these hoods offer high reliability performance for the most challenging design applications. A wide-range of d-sub hood systems is available, including Die-Cast, Metalized Plastic & Plastic versions. A backshell selection guide details the various options.
POWER D AND COMBO-D SUB CONNECTORS
POWER-D & Combo-D mixed contact d-sub connectors are designed for rugged / robust applications where both power & signal are required from a single connection. Power-D connectors can carry both signal (5 amp) and power (20 / 40 amp) contacts within the same connector body. Featuring “Solid-Pin” machined contacts, these connectors offer high reliability performance for the most challenging design applications.
The product range is ideal for a multitude of both IP rated and non-rated industry applications. This diverse combo d-sub product offering includes up to 13 contact configurations engineered for both power & coaxial connector environments such as satellite & weather stations, GPS receivers, transceivers and radio technology applications. Custom or semi-custom Combo-D connector solutions are also available[JH14] ; these are suitable for applications with modules with unique combinations of signal and power pins, such as robotic work cells.
COAXIAL D-SUB CONNECTORS
Coaxial D-Sub connectors are available in 5 standard shell sizes with 11 multiple contact arrangements. These reliable, robust combination d-sub connectors allow a combination of signal and coaxial contacts in cable mount, vertical board mount & right-angle board mount termination type variations.
CUSTOM CONNECTORS
Although there are numerous types of standard connectors, they do not satisfy every application. In such a custom connector and cable solution is often the answer. Examples of one-of-a-kind designs include:
- Custom connector system for testing a handheld engine and diagnostic system for home construction machinery
- Custom cable assemblies for intelligent battery analyzers and charging systems for the wireless, mobile computing, medical, and transportation industries
- Modification of the standard production flow for D-sub connectors resulting in a unique solution for an industrial customer.
See more custom solutions here. Contact NorComp for more information.
CONNECTOR APPLICATIONS
Not every connector meets every application requirement. This section discusses the needs of the primary application areas and provides recommendations for the most suitable connectors.
CONNECTORS FOR COMMUNICATIONS APPLICATIONS
Robust connector and cable assembly solutions are crucial to optimize performance across communications applications in data and network servers, routers, monitors, storage systems, support equipment, and other computer peripherals.
RECOMMENDED CONNECTORS
Recommended connector families for data and communication applications include VULCON™ and QUIK-LOQ™ circular connectors; POWER-D and COMBO mixed connectors; and MICRO-D connectors and cable assemblies.
CONNECTORS FOR INDUSTRIAL APPLICATIONS
As automation increases and applications add internet connectivity, there is more pressure than ever before to develop reliable and robust interconnected production and motion control systems. Examples of common industrial applications include Industrial robotics; Automotive manufacturing; Food & beverage processing; semiconductor manufacturing; process control systems; and many others.
The industrial environment is particularly challenging for connectors. Industrial applications subject connectors to mechanical stresses such as extreme temperatures, vibration, shock, or pressure; chemical stresses such as salt water or corrosive chemicals; and a range of electrical stresses.
RECOMMENDED CONNECTORS
Industrial connector products include both standard and custom solutions that are engineered with highly reliable contact technologies that maximize operating efficiency and manufacturing uptime.
There are also application-specific industrial connector solutions and matching cable assemblies for industries such as assembly line automation, food and beverage, material handling, and commercial vehicles.
CONNECTORS FOR MEDICAL APPLICATIONS
Medical connection systems (cables and connectors) are used to transmit power, data, and control signals to and from medical devices. They can be found in numerous clinical settings: surgical devices such as hand tools; therapeutic equipment; and diagnostic equipment such as EEG, ECG, EKG & EMG machines. They are also common on portable medical devices.
Medical connectors must withstand various medical sterilization processes including autoclave, Sterrad, EtO, gamma and chemical sterilization. A medical interconnect system must also be sealed against water and dust and other potential hazards. Other requirements include: a high mating cycle, IP rating up to IP68, good EMI / RFI performance: and quick connect/disconnect capability. Certain medical applications may have specific requirements.
RECOMMENDED CONNECTORS
Medical connectors must demonstrate high dependability, corrosion-resistance, and high reliability. Recommended connector families include flanged waterproof d-sub connectors; VULCON™ and QUIK-LOQ™ circular connectors; and MICRO-D and POWER-D connectors.
CONNECTORS FOR MILITARY APPLICATIONS
In many cases (communications, for example) the pace of development in the commercial sector has outpaced that in the military sector, resulting in more powerful capabilities at lower cost. To reap some of the benefits, military applications look to commercial off the shelf (COTS) technology that can meet their stringent requirements.
M24308 is a US military standard for D-sub connectors. Typical M24308 d-sub connectors include ruggedized tablets and laptops, voice and data communication systems, GPS receivers and hubs, and portable power supply units.
Mil-COTS connectors are expected to withstand high impact shock, corrosion, & extreme changing temperatures, as well as other combat conditions. They are designed to operate over a wide temperature range.
RECOMMENDED CONNECTORS
NorComp is an ITAR (International Traffic in Arms Regulations) registered & certified manufacturer of COTS equivalents to M24308 d-sub connectors for military applications. See the cross reference list here for the complete product range of NorComp MIL-COTS, equivalent to M24308 connectors.
CONNECTORS FOR ROBOTICS APPLICATIONS
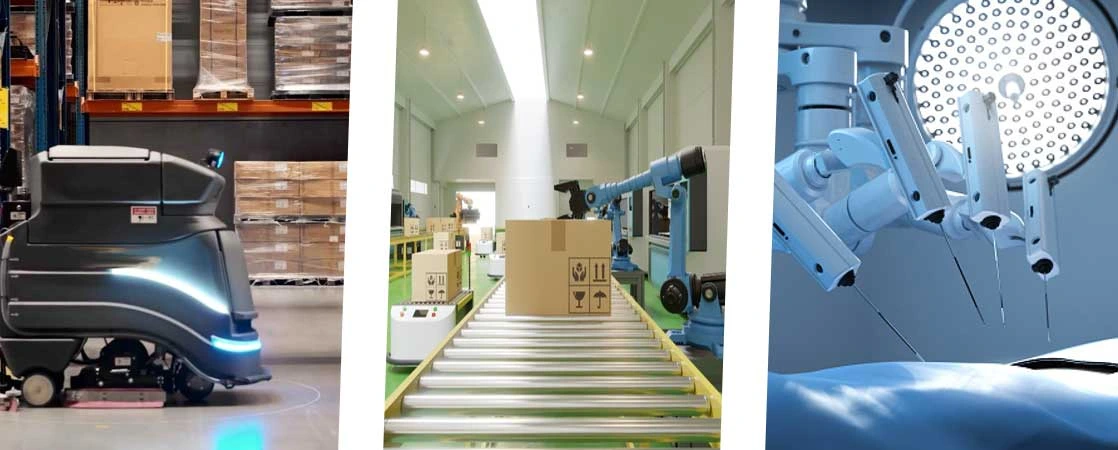
Industrial robotic devices are highly complex electro-mechanical machines that may contain multiple computers, dozens of sensors, hydraulic pumps, multiple motors, and connections to a network. The technology trend is drive toward reduced size, weight, and power consumption, as well as increased connector throughput. More specialized robots for the military, food, pharmaceutical, and medical industries are becoming available.
Connectors in robotics applications are exposed to many of the same conditions as other industrial machines: high temperatures, high voltage spikes, moisture, dust, industrial fumes as well as shock and vibration.
RECOMMENDED CONNECTORS
Products suitable for the robotics market include MICRO-D connectors and cable assemblies: waterproof d-sub connectors; push-pull connectors; and VULCON™ circular connectors.
RUGGED ENVIRONMENT CERTIFIED CONNECTORS
Many types of connectors must operate in rugged or harsh environments. Some characteristics of rugged environments are:
- Temperature extremes
- Pressure
- Shock & Vibration
- Explosion risk
- Corrosion
- Rough handling
Many applications experience multiple environmental hazards, as shown in the following table.
Application | Temperature | Shock/ Vibration | Pressure | Corrosion | Explosion | Liquids | Dust |
Medical | X | X | X | ||||
Automotive | X | X | X | X | |||
Industrial | X | X | X | X | X | X | |
Oil & Gas | X | X | X | X | X | X | X |
Agricultural | X | X | X | X | X | ||
Marine/Undersea | X | X | X | X | X |
Several key design features provide a connector with protection from harsh environment hazards.
- Locking/coupling mechanisms. A robust coupling mechanism is a must for harsh connectors.
- Housing and insulation For applications where the connector is likely to be exposed to extremes of temperature and plenty of moisture and dust, a corrosion-resistant metal housing may be the most appropriate option. For other uses requiring lightweight and flexible connectors, high-temperature resistant plastic composites may be more attractive
- The shape of the connector, thread pattern or mating mechanism and positioning of pins also play an important role in the creation of a rugged and reliable connector. Circular connectors allow for easier connection and disconnection. They are also easier to seal and less likely to wear or break.
RECOMMENDED CONNECTORS
Rugged Environment Certified (REC) is an external testing certification that reinforces the quality and performance of ruggedized harsh-environment connector solutions. These products have been proven to withstand the most challenging environments given use in many outdoor harsh environments including oil rigs, weather stations, & ruggedized industrial applications.
CONNECTORS FOR TELEMATICS APPLICATIONS
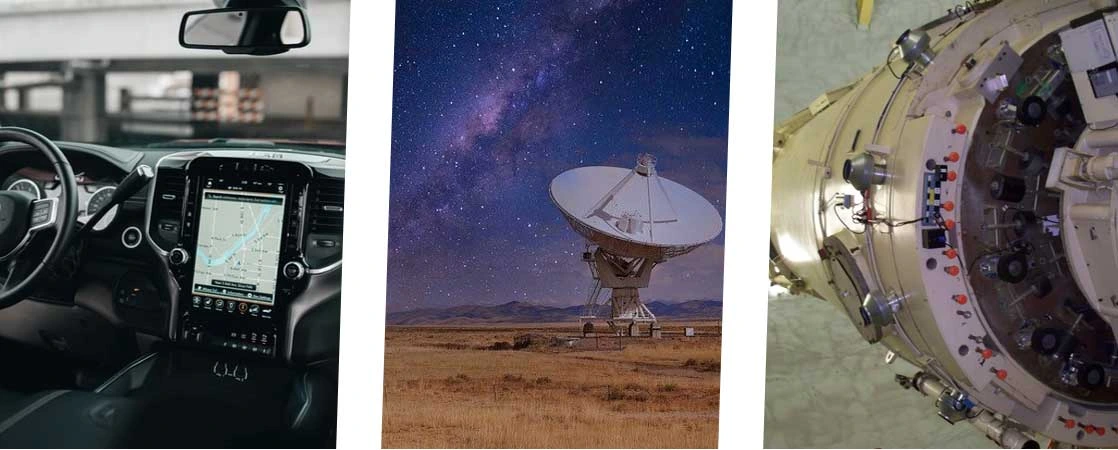
Telematics deals with the long-distance transmission of computerized information. The field encompasses areas such as emergency warning systems for vehicles, GPS navigation, onboard diagnostic (OBD) applications, vehicle tracking, and fleet management devices. These applications all require a secure, reliable connection critical for the precision of the telematics technology reporting.
Connectors for telematics must operate in harsh environments in the presence of moisture and vibration. Telematics applications often require both power and signals to be sent over a single connector; in addition, the connector must be capable of regular connection and disconnection cycles.
RECOMMENDED CONNECTORS
The SEAL-D® connector family offers a variety of solutions to the challenges encountered in ruggedized telematics applications. NorComp’s proprietary sealing process provides IP67 protection while maintaining industry standard connector footprints and panel space requirements. SEAL-D® connectors are available in both signal-only (up to 44 contacts) & Combo-D configurations that offer both signal and power contacts in either 20-amp or 40-amp options.
Other connector families suitable for telematics applications include VULCON™ M-series circular connectors; Power-D and Combo Mixed connectors; and QUIK-LOQ™ circular push-pull connectors.
CONNECTORS FOR TEST & MEASUREMENT
Measuring devices to monitor and control processes are critical to the smooth operation of large systems and operating efficiencies. Since both high-speed digital and low-level analog signals are often present, the connector or cable assembly must be properly shielded to prevent any hint of interference.
RECOMMENDED CONNECTORS
Standard product families suitable for test & measurement include MICRO-D connectors and cable assemblies; waterproof d-sub connectors; QUIK-LOQ™ circular push-pull connectors; and VULCOM™ M-series screw thread connectors.
We also offer custom and semi-custom solutions for unique custom interconnect projects.
CONNECTORS FOR TRANSPORTATION APPLICATIONS
A wide range of connectors are used in mass transit, railway, off-road heavy equipment, and commercial marine applications. Heavy equipment for off-highway transportation must withstand the demanding applications with a rugged, robust connection resistant to mud and corrosion.
Connectors for transportation applications must accommodate extremely harsh environments while maintaining a high-performance connection. These connectors are also essential for applications that require high reliability, such as lighting, doors, sensors, and brakes.
RECOMMENDED CONNECTORS
The transportation market is served by a variety of off-the-shelf connectors from the existing product catalog. Examples include waterproof d-sub connectors; Power-D and Combo Mixed connectors; QUIK-LOQ™ circular push-pull connectors; and VULCOM™ M-series screw thread connectors.
Many applications also require customized connector solutions, especially in rail and aviation.
RESOURCES
The NorComp website has several resources for those wishing to learn more about the various types of connectors and recommendations for their use. Resources include:
Recommended connectors for different applications
Environmental Compliance statements
White Papers: Custom project success stories
Contact us for more information.