Products
- Circular Connectors & Cable Assemblies
- D-Sub Connectors
- IP67 D-Sub Connectors
- D-Sub Backshells
- Micro-D Connectors & Cable Assemblies
- Power-D & Combo Mixed Connectors
- Push Pull Connectors
- D-Sub & Micro D Hardware
- Modular RJ45 Connectors
- USB Connectors
- D-Sub Adapters & Gender Changers
- SCSI .085"/.050"
- .050 Ribbon
- Headers & Receptacles
- Bayonet Connectors
What IP Ratings Don’t Tell You About Ruggedized Connectors
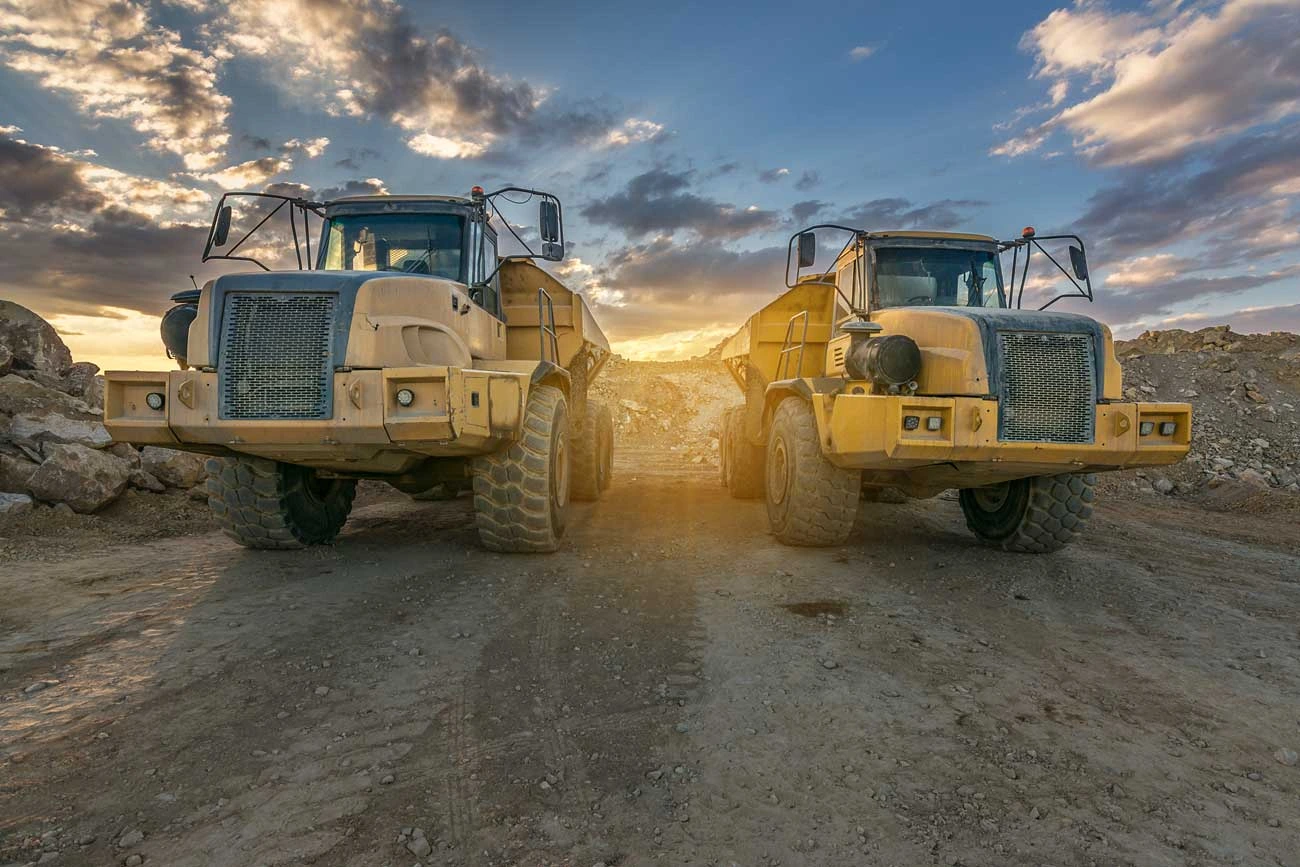
When discussing ruggedized electronics equipment and harsh environments, IP ratings are always a key part of the conversation. The international standard is useful in many types of applications: industrial, telematics, sensors, robotics, automation, oil and gas, marine/undersea, automotive, and Internet of Things. But IP ratings shouldn’t be taken as the whole story. There’s more to consider when choosing and designing electronics equipment, right down to the connectors you choose. Because they play key roles in routing signals and power within and between devices and modules.
The importance of IP
IP (ingress protection) is a measure under the international IEC-60529 standard of specifically how well protected a device or component is from environmental hazards. The codes start with the IP label and are followed by two single-digit numbers. The first digit indicates protection against solid particles. The second, how long the item can exclude liquids.
For example, the “6” in the common IP67 rating means that the item is protected against all dust as proven with an extended test under vacuum conditions. Meanwhile, the “7” means the item can withstand immersion in water at between one to three meters for at least 30 minutes.
But an IP rating provides only limited information about resistance to particulates and liquids. For one thing, a higher rating doesn’t necessarily mean better performance. That “7” in IP67 only covers immersion, for example. It doesn’t provide any data on resistance to high pressure jets of water, which are covered in categories 6 and 9. Plus, the immersion testing is done with fresh water—so the results may not apply to water containing salt, chlorine, or other chemicals.
And IP ratings don’t address other aspects of harsh environments: temperature extremes, shock or vibration, corrosion, rough handling, or even explosion risk. Smart design choices require additional information.
Other ruggedized factors
Designers should consider other systems that address additional factors that might be important for a project. UL Solutions has several standards for electrical connectors: UL 1977, UL 2238, and UL 2237. They include 10 different considerations, including:
- Where assembly happens
- The types of applications
- Whether the connector is for OEMs only or for commercial and industrial use
- Maximum voltage
- Current ratings
- Whether it’s intended for current interruption under load conditions
- If it requires a short circuit current rating, and the type of connection
Then there’s the world of mil-spec requirements and the need for commercial off the shelf (COTS) connectors that can work with such military-use devices as tablets, laptops, voice and data communications, GPS receivers and hubs, and portable power supplies. There are multiple specifications that can come into play and something for military applications has to meet all the applicable requirements.
Avoiding impact on the environment
Rather than looking at susceptibility of a device to the environment, this is about restricting the impact a device could have on an environment, like a form of inverse ruggedization. The Restriction of Hazardous Substances (RoHS) standard comes out of the EU and specifies the maximum levels of ten different materials: cadmium, lead, mercury, hexavalent chromium (Cr VI), polybrominated biphenyls (PBB), polybrominated diphenyl ethers (PBDE), Bis(2-Ethylhexyl) phthalate (DEHP), benzyl butyl phthalate (BBP), dibutyl phthalate (DBP), and Diisobutyl phthalate (DIBP).
There are many other areas of material compliance, whether use of asbestos, certain materials from geopolitical conflict zones, DEFARS U.S. defense acquisition restrictions on specialty metals, ozone depleting certifications, compliance with the Toxic Substances Control Act of 1976, and more.
Device reliability versus certification red tape
Having connectors with the desired certifications can be good, but the question is the price that will entail. There are significant expenses to gaining certifications and vendors must recoup the amounts by charging more for their devices.
For designers and engineers, depending on the type of client, there will be times when specifications will require component-based certifications. However, many aren’t interested in specific certifications of individual components but rather for the end design to meet performance and condition criteria.
Frequently there are available connectors that will perform as needed, with equal quality and the only difference lack of official certification. Such equivalent performance devices will save money in procurement and production. Look beyond certifications and to vendors you can trust to deliver connectors that provide the specifications you need.
NorComp offers both standard and custom solutions and has experts available to help you find what you need.
Go Back