Connectors for Rugged Outdoor Sensor Applications Table of Contents:
- WHAT IS A SENSOR AND HOW IT IS USED?
- WHAT ARE SOME RUGGEDIZED SENSOR APPLICATIONS?
- ENVIRONMENTAL MONITORING AND LOGGING:
- TRAFFIC MONITORING & CONTROL:
- OIL / GAS / WATER:
- AUTOMATED MANUFACTURING
- THE ENVIRONMENT FOR OUTDOOR SENSOR CONNECTORS
- CONNECTORS FOR RUGGED OUTDOOR SENSOR APPLICATIONS
- RECOMMENDED CONNECTORS FOR RUGGED SENSOR APPLICATIONS
- COAXIAL D SUB CONNECTORS
- CUSTOM CONNECTORS
- RESOURCES
Connectors for Rugged Outdoor Sensor Applications
Sensors in the marine, oil and gas, telematics, electric power, off-road heavy equipment, railway, agriculture, mass transit, data logging, and other industries must operate with high reliability in rugged outdoor environments. Connectors that interface to sensors in these conditions must satisfy a stringent set of electrical, mechanical, and environmental requirements.
This pillar page will discuss the functions performed by sensors, some of the applications where they are used. It will then review the environmental requirements for connectors used in those applications and the recommended NorComp connectors. Finally, the pillar page will include a list of useful resources for engineers who must choose the optimum connector for their outdoor sensor project.
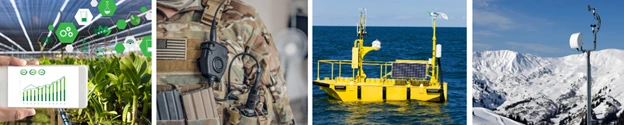
What Is A Sensor And How It Is Used?
The function of a sensor is to measure a physical quantity and translate it into an electrical signal so that it can be logged, analyzed, or used in a control system.
Depending on the type of sensor, its output signal can be voltage, current, resistance, or some another electrical attribute such as capacitance. Some sensors are available with digital outputs and output a series of bytes of scaled or unscaled data. Pure analog sensors typically supply their output to a data acquisition system.
A digital sensor often bundles a communications interface, such as RS-232 or USB into a single package. Similarly, many analog sensors integrate signal-conditioning electronics into a single module.
Numerous types of sensors are used in outdoor applications. Examples include:
Sensor |
Physical Quantity Measured |
Thermocouple, RTD, Thermistor |
Temperature |
Strain gauge |
Pressure, tension, weight |
Load cell |
Weight and load |
LVDT sensor |
Displacement in distance |
Humidity sensor |
Water vapor |
Accelerometer |
Vibration, shock, position |
Microphone |
Sound |
Current transducer |
AC or DC current |
Voltage transformer |
High voltage potentials |
Optical sensor |
Light |
Camera sensor |
Single and continuous 2D images |
Digital encoder |
Rotating on/off signals |
Radar sensor |
Microwave signals |
Lidar sensor |
Laser light |
Positioning sensor (GPS) |
Longitude and latitude from GPS or similar |
Radiation sensor |
Solar radiation, ionizing particles |
What Are Some Ruggedized Sensor Applications?
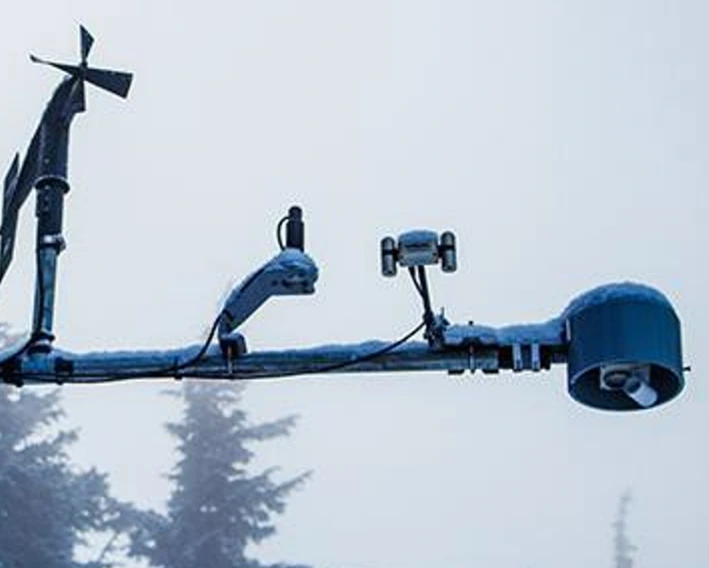
There is a wide variety of sensor applications. They can measure environmental conditions such as wind speed, humidity, temperature, or soil moisture. They can monitor operating conditions in a process control system or a water treatment plant. They can also perform safety functions such as detection of a human or foreign object in the envelope of a robotic work cell, or monitoring radiation levels in a nuclear power station.
Sensors are an integral part of real-time control applications, too. Sensors are used in process control systems to help regulate chemical mixtures or fluid flow. They provide measurements of speed, torque, and position for precision motor controllers. And radar or lidar sensors are in every autonomous vehicle to help it form a 3-D image of its surroundings using time-of-flight measurement.
The same sensors can be used in both benign and rugged environments. Load cells, for example, are used in bathroom scales as well as commercial truck weigh stations. And temperature sensors are found in everything from home medical kits to aircraft engines.
Many applications use large numbers of sensors. An automobile, for example, uses hundreds of different sensors, including oxygen sensors in the engine, acceleration sensors in the airbag controller, radar sensors for collision avoidance, and ultrasonic sensors for parking. These sensors must operate flawlessly for years in the harsh automotive environment. A robust connector is key to maintaining high levels of performance.
Here are some examples of rugged-environment applications with the types of sensors that they typically contain.
Environmental Monitoring And Logging:
- Weather Stations
- Solar Radiation Sensors
- Temperature Sensors
- Wind Speed / Direction Sensors
- Rainfall Sensors
- Humidity Sensors
- Farming (Outdoor & Indoor)
- Radiation Sensors
- Humidity Sensors
- Soil Sensors (soil moisture or nutrients)
- Smart Buoys (Oceans & Rivers)
- Wave Height, Period & Power Sensors
- Water & Air Temperature Sensors
- Barometric Pressure Sensor
- GPS Location Sensor
Traffic Monitoring & Control:
- Stoplight Controls
- Lidar Sensors
- Radar Sensors
- Optical Sensors
- Speed, Volume & Pattern Monitors
- Same as above
Oil / Gas / Water:
- Well Head / Tank Farms
- Pressure Sensors
- Flow Sensors
- Distribution Networks
- Pressure Sensors
- Flow Sensors
- System Status / Integrity Sensors
Automated Manufacturing
- General Machine Status / Integrity
- Temperature Sensors
- Pressure Sensors (Pneumatics / Hydraulics)
- Optical Sensors
- Actuators / Implements
- Position Sensors
- Pressure Sensors
- Optical Sensors
- Infrared Sensors
- Proximity Sensors
Many other applications exist; the list above is only a sample. Telematics uses sensors on construction sites for tracking the location of heavy equipment and preventing theft. Smart shipping containers log position with GPS sensors, and monitor internal conditions: for example, to ensure that vaccines do not exceed their storage temperature. And of course, the military and aerospace industries are both prolific users of sensors in rugged conditions.
The Environment For Outdoor Sensor Connectors
Connectors play a key role routing signals and power between almost all electronic systems from smartphones to spacecraft. In an application that uses sensors, connectors provide the interface between the sensor module and the next stage in the signal chain.
They also protect the sensor and its electronics from the harsh outdoor environment. In this case, the connector not only provides a reliable transfer of signals and power; it also must maintain the integrity of the sensor design to protect against the intrusion of liquids and dust.
Sensor connectors in outdoor applications are subject to two types of stresses: those due to the outdoor environment and those due to the application itself. Stresses related to outdoor operation can include extreme hot and cold temperatures, temperature cycling, dust, humidity, and moisture including salt spray. Application-related stresses can include all of the above, plus vibration, shock, high pressure, corrosive chemicals, and a range of electrical stresses.
Let’s look at some of these stresses in more detail and their effects on connectors.
* Temperature extremes. The majority of environmentally-caused failures are due to excessive temperature or temperature cycling. Most are a result of thermal stress brought on by differences in the coefficients of thermal expansion (CTE) of different materials.
Temperature extremes also affect a connector’s mechanical components. Rubber seals and plastics tend to harden and resist deformation, causing leaks or cracks. Designs must often operate reliably in both hot and cold environments. The weather station in figure 2, for example, is installed in environments that range from winters in northern Canada to summers in Death Valley.
* Shock & Vibration are common features of many outdoor applications. They can cause mechanical stress in connectors, which results in solder joint cracks, loosening of screws and other fasteners, and metal fatigue. Sensor connectors on mobile machinery are continuously subject to these mechanical stresses.
* Explosion risk is a concern in oil & gas, coal mining, and wood processing operations. Flammable gases, vapor, dust, or powder are common features of these environments. In such conditions, the making or breaking of a contact – by unplugging a connector, for example - may result in a spark with catastrophic results.
* Rough handling. Many sensor connectors, especially those on portable equipment, are connected and disconnected multiple times in a day, often hurriedly, which increases the risk of wear and tear on the connector. Connectors being dropped or dragged along hard surfaces can damage internal components and can affect the integrity of power or data signals.
* Corrosion caused by exposure to chemicals is an everyday occurrence in outdoor environments. The most common combination is high relative humidity coupled with salt fog, which can wreak havoc with electronic components and connectors.
Different outdoor applications experience a range of environmental hazards, as shown in the following table.
Application |
Temperature |
Shock/ Vibration |
Corrosion |
Explosion |
Liquids |
Dust |
Telematics |
X |
X |
X |
X |
X |
|
Industrial |
X |
X |
X |
X |
X |
X |
Oil & Gas |
X |
X |
X |
X |
X |
X |
Marine/Undersea |
X |
X |
X |
X |
||
Automotive |
X |
X |
X |
X |
X |
Connectors For Rugged Outdoor Sensor Applications
Sensor connectors include both standard and custom solutions that are engineered with highly reliable contact technologies that maximize operating efficiency and manufacturing uptime.
Several key design features provide sensor connectors with protection from the outdoor environment.
- Locking/coupling mechanisms. A robust coupling mechanism is a must for connectors to maintain connectivity in all conditions.
- Housing and insulation. In outdoor sensor applications the connector will likely be exposed to extremes of temperature, moisture, and dust, so a corrosion-resistant metal housing may be the most appropriate option. IP-rated connectors are preferred in many cases.
- The shape of the connector, thread pattern or mating mechanism and positioning of pins also play an important role in the creation of a rugged and reliable connector. Circular connectors allow for easier connection and disconnection. They are also easier to seal and less likely to wear or break.
- Many outdoor applications such as cellphone towers and radar systems generate high levels of electromatic radiation. Connectors with 360° EMI shielding are preferred in such cases; examples include metal-shell push-pull connectors or D-sub connectors with metallized backshells. Both types are discussed below.
What Is Ingress Protection (Ip)?
A connector designed for rugged environments must have an IP rating appropriate to the application. The IP rating of a connector indicates the level of protection it provides against the incursion of solids, including dust, and liquids, including moisture or water. A connector’s IP rating is expressed in the form “IPXY”, where X and Y are numeric values.

The first digit in an IP rating indicates the level of ingress protection against solid objects ; from IP0x (no protection) to IP6x (complete protection against dust). The second digit refers to protection from liquids: from IPx0 (no protection) to IPx9 (protection against water jets). Ruggedized connectors are tested to a variety of IP standards: IP50, IP66, IP67, or IP68.
A connector shown as Rugged Environment Certified (REC) indicates that it has been proven in the field to withstand the most challenging environments including oil rigs, weather stations, & ruggedized industrial applications.
Recommended Connectors For Rugged Sensor Applications
This section covers products recommended for rugged outdoor sensor applications. Of course, sensors operating in industrial robotics, automated assembly lines, welding, etc., must cope with the same harsh conditions as the applications described above: the same connectors are also suitable for these applications.
Most complex applications require numerous types and sizes of connectors. The connectors on the weather station mentioned above, for example, range from small connectors on individual sensors to larger connectors on the data logger located at the base of the weather station tower.
Recommended connector families include Micro-D connectors and cable assemblies: VULCON™ circular connectors; waterproof d-sub connectors; and QUIK-LOQ™ push-pull connectors.
Metric Circular Connectors
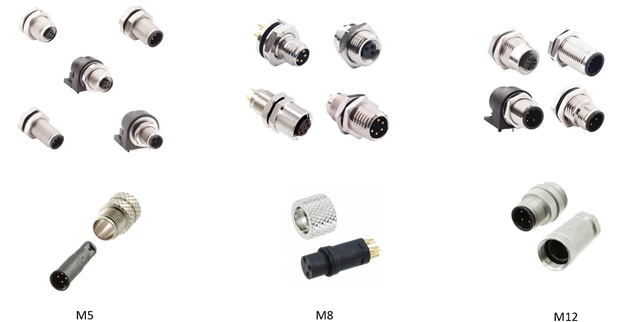
VULCON™ metric circular connectors (Figure 3) have screw threads and conform to the DIN EN 61076 standard. These connectors offer a robust waterproof cable-to-panel or cable-to-PC board interface for and take up less room than rectangular style connectors with the same pin count, maximizing the use of mounting space. The numerous cabling and pin options have made these circular connectors popular in multiple outdoor applications due to their flexibility, ruggedness, and reliability. The number after the M indicates size, from small to large.
M12 Circular Connectors
The M12 circular connector has become a leader for sensor applications due to its ability to endure stressful environments and protect against dust while remaining waterproof. M12 sensor applications include automation, remote process sensors, robotics control systems, ruggedized networking, & power conditioning systems. VULCON™ M12 connectors are now available in an upgraded stainless steel version for the most rugged outdoor applications. These connectors feature IP67/68 ratings and stock packages are available for rapid prototyping.
M8 Circular Connectors
The M8 circular connector quickly made its debut as a smaller more compact version of the M12. M8 connectors are used in applications requiring a rugged and robust fully shielded metal shell able to withstand shock and high vibration. M8 outdoor applications include ruggedized data loggers & sensors, electronic gauges & metering, avionics, and marine electronics.
M5 Circular Connectors
M5 connectors are ideal for many applications where a rugged and compact connector solution is required to deliver a secure and reliable signal transfer. M5 connector applications include sensor connectivity applications in transportation and control systems.
All metric circular connectors feature IP67/68 protection and are rated over the -40 °C to +85 °C temperature range. The table below shows the options available for each type.
Connector |
Contact Count |
Type |
Shield |
M5 |
2,3,4 |
cable mount, panel mount |
Shielded, unshielded |
M8 |
3,4,5,6 |
cable mount, panel mount |
Shielded, unshielded, cable kit |
M12 |
3,4,5,6,8,12 |
cable mount, panel mount, anti-vibration |
Shielded, unshielded, cable kit |
Outdoor sensor applications can use connectors with a variety of connector counts. The smaller connectors might be used with a single sensor; a larger connector might be used to send signals and power between a sensor module and a data acquisition system.
Push Pull Connectors
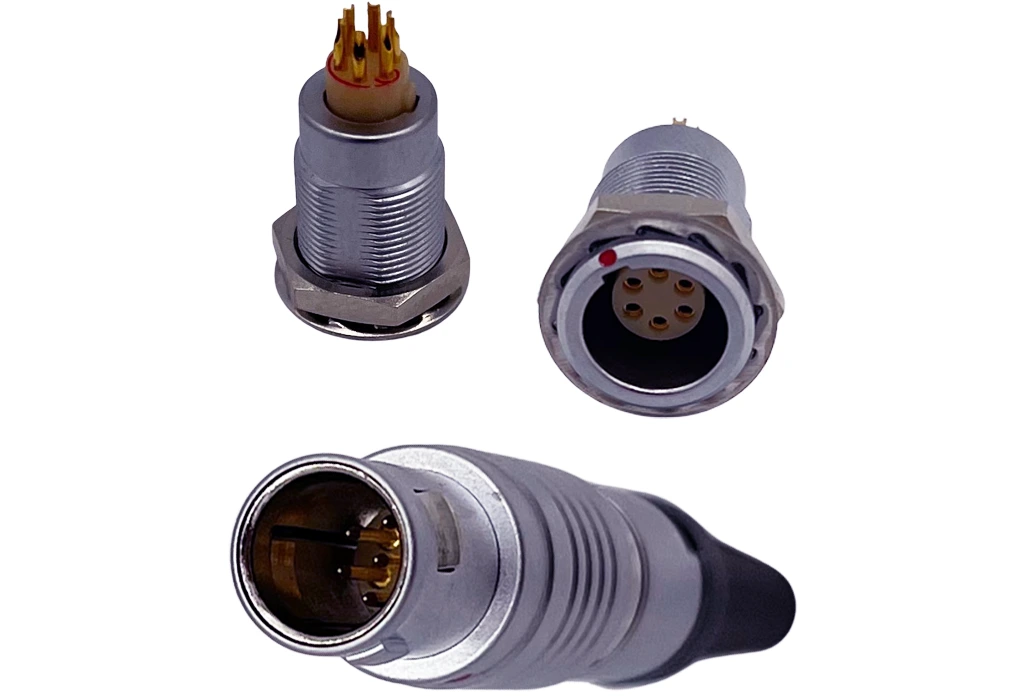
QUIK-LOQ™ Circular Push-Pull Connector systems (figure 4) are rugged, sealed connectors ideal for high-reliability waterproof applications where quick connect / disconnect and environmental protection are required. These connectors provide a convenient solution for sensor systems such as dataloggers that must handle a variety of sensor types. Push-pull connectors are rated to REC standards and can withstand high levels of shock and vibration.
There are several families of QUIK-LOQ™ connectors. Features and benefits include:
- Rapid latching release mechanism with alignment key
- Small, rugged precision design
- Available in varying pin positions
- Accepts 14-28 awg wires (based on # of positions)
- Rated for 2 to 30 amps depending on # of positions
- High Mating Cycles (>5000)
- Machined contacts and housing
- 360° shielding for full EMI / RFI
Metal Shell Push Pull Connectors
QUIK-LOQ™ IP50 Push Pull Connector systems are ideal for sensor applications where high mating cycles & quick connections are called for. The rugged IP50 Push Pull Connectors are engineered with machined contacts and housing for optimal connectivity.
QUIK-LOQ™ IP67 Push Pull Connector Systems are rated for more than 5,000 mating cycles and include alignment keys and rapid latching & release mechanisms. The series features 360° EMI/RFI shielding, and precision-machined contacts for the most reliable signal transfer in heavy-duty environments.
Standard D-Sub Connectors
The D-type connector has been used in many applications as a multi-way connector and is well-known as the connector used for RS-232 serial links, although industrial Ethernet or CAN are more common in industrial and outdoor applications.
Nonetheless, D-subminiature connectors, d-sub backshells, & hoods are still widely used for sensor applications that require a rugged, robust I/O connector system. D-sub connectors are available in solder cup, crimped, and IDC versions depending on model.
There are several families of D-sub connectors. Economical standard D-Sub connectors are available in sizes ranging from 9 pins to 50 pins. These are offered with nickel or tin shells with either crimp or snap-in contacts. High-density D-sub connectors offer 65% greater pin density than the standard models and are available with 15 to 78 pins.
MICRO-D Connectors
Machined Micro-D connectors are less than one-third the size of standard d-subs and are designed for space-constrained applications that still need a rugged I/O connector system.
There is a full range of micro-d connectors in 9-pin, 15-pin, and 25-pin configurations with both cable & board mount options. Features include a metal-to-metal interface for robust mechanical connections and effective shielding, a contact rating of 2 amps, and operation over a temperature range of -40°C to +125°C.
IP Rated D Sub Connectors
SEAL-D® connectors are designed for sensor applications that require protection from heavy spray or are exposed to short-term submersion. The IP67 rated waterproof d-sub connectors (figure 6) are sealed internally and maintain the same footprint as the standard d-sub product offering. This IP sealing technology allows any existing d-sub product to be manufactured in an IP67-rated version.
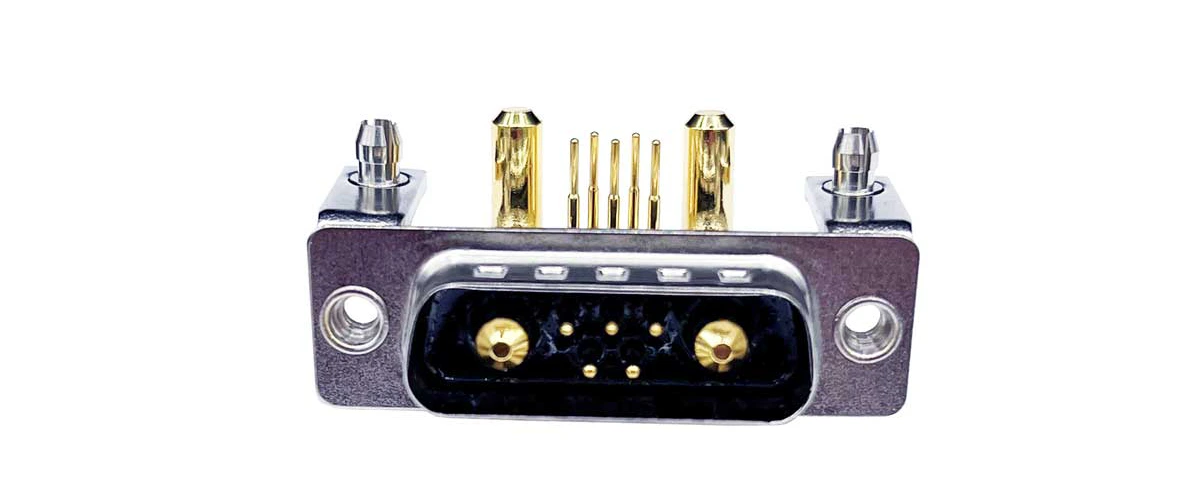
SEAL-D® connectors are available in vertical and right-angle board mount types as well as solder cup for panel mount cable applications. Standard D-Subs are available in 9 pin, 15 pin, and 25 pin positions, and high density D-Subs are available in 15-pin, 26-pin, and 44-pin positions. Examples of sensor applications include:
- Remote sensors, gauges, and data loggers that are exposed to the elements
- Outdoor equipment that is routinely subject to wash down
The SEAL-D® family are drop-in replacements for standard unsealed connectors; this eliminates the need to change PCB and sheet metal designs when upgrading to IP67 standards.
NANOOK
flanged waterproof d-sub connectors provide robust IP67-rated performance in standard, high-density, and mixed layout configurations, NANOOK connectors are reliable, cost effective, and operate over a -25°C to +85°C temperature range.
D Sub Backshells
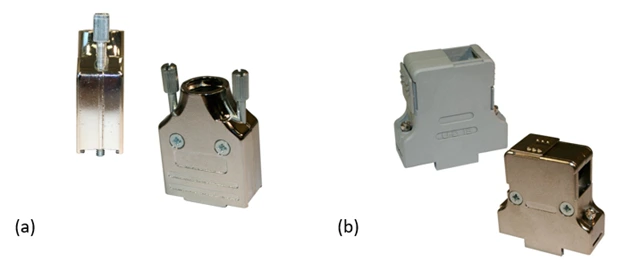
D-sub backshells are designed to maximize EMI/RFI shielding for optimal protection and performance. The comprehensive product offering features a variety of options that improve the connection stability while maximizing cable strain relief to prevent damage to wires and contacts.
ARMOR D-Sub hoods are designed for rugged / robust sensor applications including military, industrial, and aerospace sensors. Featuring an all-metal hood diecast housing, these hoods offer high reliability performance for the most challenging design applications. A wide range of d-sub hood systems is available, including Die-Cast, Metalized Plastic & Plastic versions. A backshell selection guide details the various options.
POWER-D And Combo-D Sub Connectors
POWER-D & Combo-D mixed contact d-sub connectors are designed for sensor applications where both power & signal are required from a single connection. Power-D connectors can carry both signal (5 amp) and power (20 / 40 amp) contacts within the same connector body. Featuring “Solid-Pin” machined contacts, these connectors offer high reliability performance for the most challenging design applications.
The product range is ideal for a multitude of both IP-rated and non-rated sensor applications. This diverse combo d-sub product offering includes up to 13 contact configurations engineered for both power & coaxial connector environments such as satellite & weather stations, GPS receivers, transceivers, and radio technology applications. Custom or semi-custom Combo-D connector solutions are also available; these are suitable for applications with modules with unique combinations of signal and power pins, such as robotic work cells.
Coaxial D Sub Connectors
Coaxial D-Sub connectors are suitable for outdoor audio, video, and RF applications. Available in 5 standard shell sizes with 11 multiple contact arrangements, these reliable, robust connectors provide a combination of signal and coaxial contacts for cable mount, vertical board mount & right-angle board mount terminations.
Custom Connectors
Although there are numerous types of standard connectors, they do not satisfy every sensor application. In such cases, a custom connector and cable solution is often the answer. Examples of one-of-a-kind NorComp designs include:
- Custom connector system for testing a handheld engine and diagnostic system for home construction machinery
- Custom cable assemblies for intelligent battery analyzers and charging systems for the wireless, mobile computing, medical, and transportation industries
- Modification of the standard production flow for D-sub connectors resulting in a unique solution for an industrial customer
See more custom solutions here. Contact NorComp for more information.
Resources
The NorComp website has several resources for those wishing to learn more about the various types of connectors recommended for outdoor sensor applications. Resources include:
Rugged Environment Certified connectors
Transportation industry connectors
Environmental Compliance statements
White Papers: Custom project success stories
Click on the links or contact us for more information.