Products
- Circular Connectors & Cable Assemblies
- D-Sub Connectors
- IP67 D-Sub Connectors
- D-Sub Backshells
- Micro-D Connectors & Cable Assemblies
- Power-D & Combo Mixed Connectors
- Push Pull Connectors
- D-Sub & Micro D Hardware
- Modular RJ45 Connectors
- USB Connectors
- D-Sub Adapters & Gender Changers
- SCSI .085"/.050"
- .050 Ribbon
- Headers & Receptacles
- Bayonet Connectors
The Future of Agriculture Automation Technology
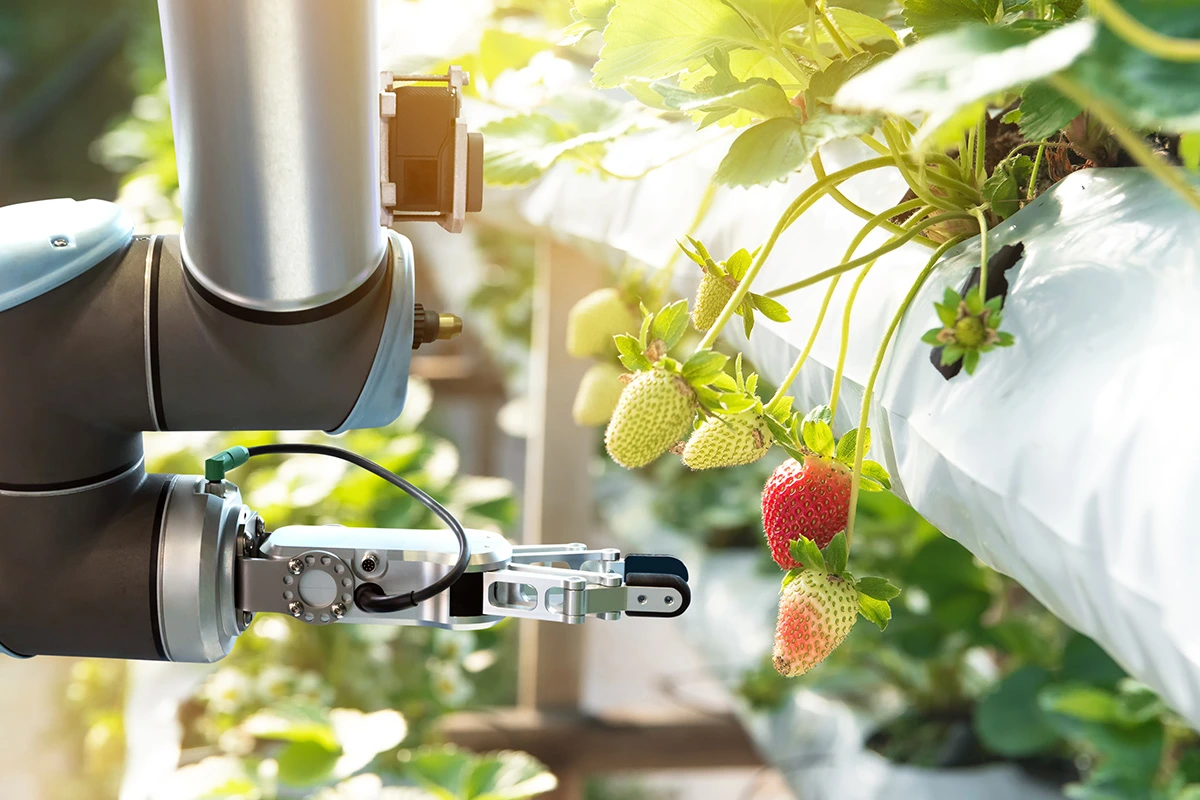
Precision harvesting reaches for the right combination of new tech
It is hard to measure the impact the invention of the combine on the 20th century. You could look at the feeding capacity of the world or the productivity of farmers, or the growth of whole industry for decades. The harvesting machine launched companies like International Harvester and John Deere into OEM giants the size and global reach of major automakers.
Although there were prototypes that could handle the three essential processes of reaping wheat (the combination in combine) in the 1920s, none could make them come to fruition until the 1940s. The No. 21 combine from Massey-Harris famously put mechanical harvesting on the map all over the United States with the Harvest Brigade near the end of WWII, when 500 machines loaned to farms produced a bumper crop of 15 million bushels of grain from more than 1 million acres.
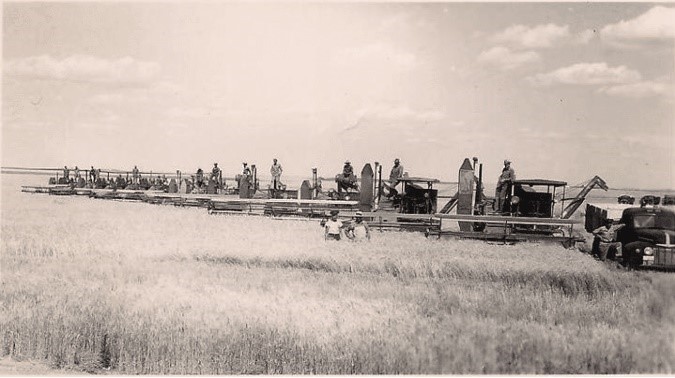
It feels like another agri-tech revolution is in the air with the prospect of precision harvesting, applied to all the crops that traditionally have been in reach only to manual laborers. Imagine thousands of acres of tomatoes, berries, peppers, cucumbers, apples, and grapes – all picked by AI-guided robotics. It is a proposition that targets $200 billion worth in fruits and vegetables per year.
Like in the 1920s and 1930s for combines, the last decade has generated a handful of startup prototypes that illustrate the potential and prove the feasibility for these more delicate and more complicated crops.
In general, analysts are bullish about the near future for precision harvesting, While the current market for the equipment is $14 billion, in five years it is expected to grow to $27.4 billion, according to a recent report. Yet today the number of specialty precision harvesting machines remains few. The new industry has yet to have its Massey-Harris moment where the upside demonstrably beats the old way of doing things.
The target of this new engineering challenge is considerably more complex than an amber wave of grain, since each fruit on the vine must be detected and then individually picked. The new combination of technologies for the next agricultural breakthrough will be mostly electronic: IoT sensors, AI image detection, and robotics:
IoT and Sensors in Agriculture
The system of remote sensors and data transmission is the most mature technology available to the new combine, since internet-of-things (IoT) and remote control of equipment is already well established in agriculture. Field sensors allow farmers to monitor their crops from any location and adjust parameters based on real-time information.
A successful autonomous harvester would need to integrate with the digital networks of the modern farm, whether Ethernet lines, RF transmission, or geolocation.
The ‘eyes’ of the operation are cameras. Some designs use a 2D RGB camera for the identification of the target in conjunction with a time-of-flight 3D camera to generate x, y, and z coordinates for the robotic arms.
Most popular connector systems for outdoor IoT sensors |
M12 Stainless Steel Connector Series | A | D | L | X | Coded |
M12 Field Wireable Connectors |
CIRCULAR CONNECTORS | M5 | M8 | M12 |
M12 T-Splitters, Y-Splitters, Straight Adapters |
How AI Can Be Used in Agriculture
Intelligent identification ripe fruit could see the most substantial refinement is in future precision harvesting.
Neural network deep learning, one branch of machine learning, has made enormous strides in facial recognition in just a few years, bringing the correct inference rate from around 70% up to near 95%. The advantage deep learning has is that it can devise its own rules for identification without the need for prescriptive criteria from humans.
The problem is a bit harder in that berries, unlike headshots, are often obscured by leaves and shadows. So far, the new combine prototypes are good at capturing the low-hanging fruit, so to speak, and miss the targets that laborers can uncover by leafing through the plants. According to a study by Monash University in Australia, robotic harvesters can generally reap 70% of the produce, while laborers follow up to pick the remaining 30%.
With such a large gap, more field testing and further ingenuity could dramatically improve the yields of the precision combine.
How are weatherproof robotics used in agriculture
The core mechanics of harvesters are borrowed from factory automation. While industrial robots typically carry out heavy-duty tasks like drilling and welding, a strawberry- or cherry tomato-gathering robot needs to have a particularly soft touch.
The approach has varied among the startups in the field, from use of more flexible materials on robotic grippers to employing scissors at the stem to minimizing handling.
And unlike a factory setting, agricultural applications require equipment to resist dirt and moisture ingress along with shockproof and survivable cabling and connectors among its multiple computers, motors, sensors, and hydraulic pumps.
Newer interconnect components on the market with reduced size, weight, and power consumption as well as increased bandwidth may supply the extra capability needed for a breakout design.
Outdoor robotic initiatives have already leveraged more rugged electronics components in all-weather conditions and extremes in temperature, such as this heavy lift drone based out of Norway. The lift utilizes specialized connectors for quick battery charging in severe climates.
Component systems properly fitted for durability and longevity will prove essential for commercial viability of future robotic harvests.
The Last Mile and Beyond
Like the wheat harvester a century ago, widespread adoption of precision harvesters could rely on an event that jars the status quo – a major labor shortage, perhaps. Alternatively, innovation on harvester systems could continue to inch forward across the last mile toward commercial viability.
In the current state of harvester robots, automation costs are on par with that of a team of laborers. The investment in small fleets made so far, however, has produced some impressive numbers. Manufacturer Traptic claims its machines can collect 100,000 strawberries per day.
Robotics for harvest may also serve as a potential platform for a host of other farm chores – weeding, pruning, and pollinating flowers – once the winning combination is found.
Go Back