Products
- Circular Connectors & Cable Assemblies
- D-Sub Connectors
- IP67 D-Sub Connectors
- D-Sub Backshells
- Micro-D Connectors & Cable Assemblies
- Power-D & Combo Mixed Connectors
- Push Pull Connectors
- D-Sub & Micro D Hardware
- Modular RJ45 Connectors
- USB Connectors
- D-Sub Adapters & Gender Changers
- SCSI .085"/.050"
- .050 Ribbon
- Headers & Receptacles
- Bayonet Connectors
Stainless Steel as a Material in Connector Technology
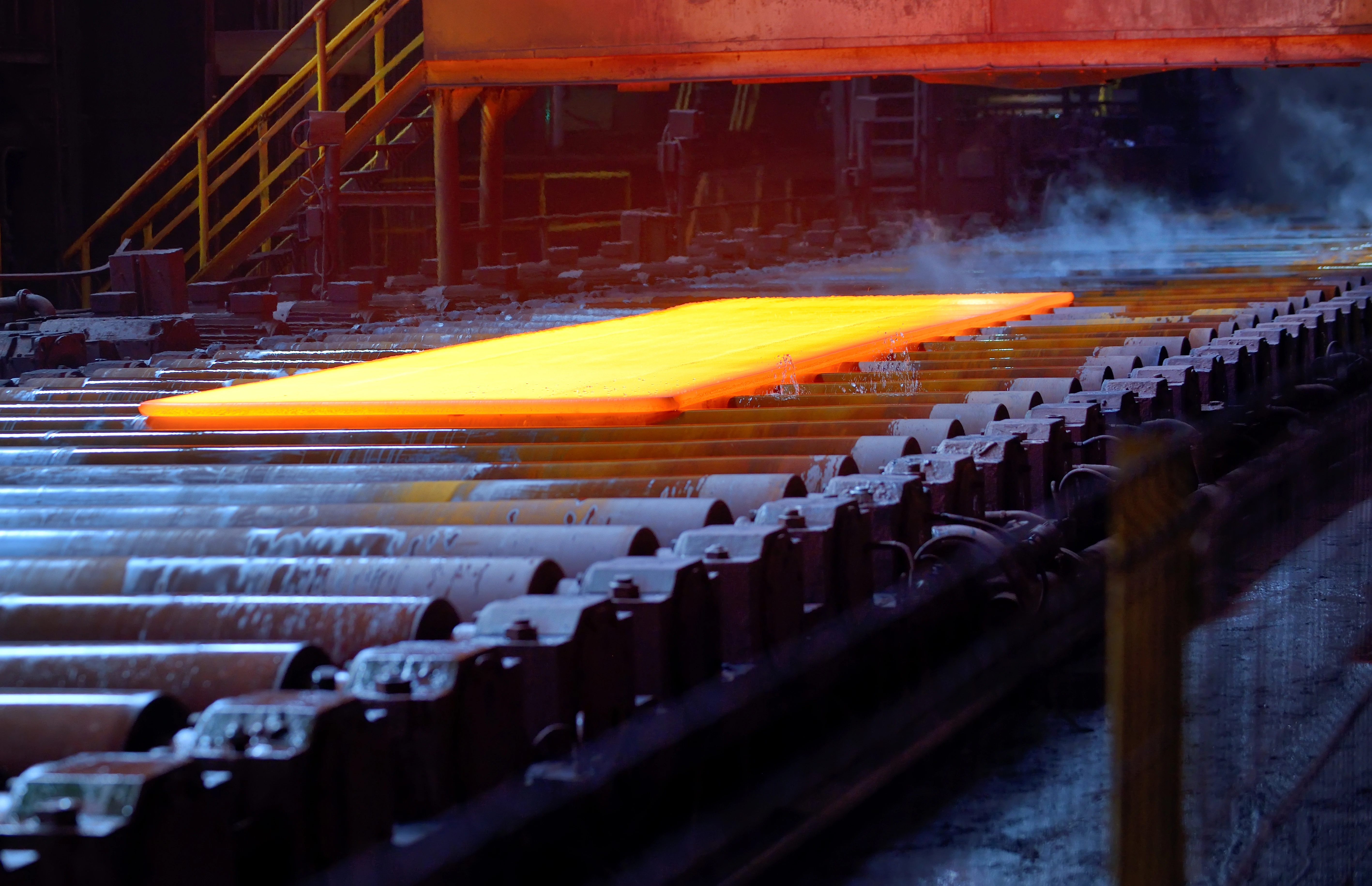
To avoid connector failure electronics designers, systems designers, process engineers, and mechanical engineers need to consider connector materials and housings. The material used in connectors determines reliability, durability, corrosion resistance, and mechanical stability in many applications. While this may seem clear-cut, in some applications–such as robotics or industrial equipment–it might seem unnecessary to use a corrosion-resistant material like stainless steel.
Stainless steel is a material of choice in certain applications where environmental stability and corrosion resistance are needed. Although other connector materials may have less weight and lower costs, they are at risk of failure in environments where exposure to corrosive substances is a potential problem.
When you’re looking for a highly reliable electrical connector that can withstand long-term exposure to contaminants or corrosive substances, consider a stainless steel option to ensure reliability and durability.
What Is the Value of a Stainless Steel Electrical Connector?
Applications and systems in aerospace, robotics, industrial systems, automotive and specialty processing equipment can greatly benefit from stainless steel electrical connectors. It’s best to consider connector options early in the design process according to the following specifications:
- Resistance to ingress of contaminants like dust or moisture
- Resistance to corrosion from liquid or gaseous substances
- Mechanical stability, specifically ability to withstand shock or vibration
- Durability compared to alternative materials like brass or plastics
Stainless steel provides value in each of these areas thanks to its mechanical strength and chemical composition. 304 stainless steel is normally preferred where lower costs and corrosion resistance are required. An alternative is 316 stainless steel, which can be used in diverse areas like marine and food service; its higher molybdenum content gives this alloy very high corrosion resistance.
Performance and Reliability Metrics
Stainless steel connectors are ideal for rugged systems as they provide greater mechanical stability and durability than hard plastics or softer metals. Stainless steel and hard plastic connectors can provide similar levels of reliability in terms of corrosion resistance, depending on the connector material and potential exposure to corrosive substances during operation.
Compared to materials like brass or aluminum, the durability and corrosion resistance of stainless steel are major advantages in some operating environments.
Thanks to the long-term durability of stainless steel connectors, including in corrosive environments, these connector/cable assemblies help simplify engineering challenges, eliminate maintenance problems, and reduce total costs over the system’s lifetime. These benefits make stainless steel electrical connectors an excellent choice in systems where corrosive substances are present or where mechanical shocks may be experienced.
Durability and Mechanical Shocks
Stainless steel is a strong metal that is much more durable than other metal connector options, such as brass. If there is a risk that a connector will be impacted by another object, stainless steel is arguably the best connector housing material to use when durability is required. While stainless steel connectors may carry higher up-front costs compared to other connector materials, the mechanical durability of stainless steel housings can eliminate maintenance and increase system lifetime, which eliminates some long-term costs.
The example push-pull stainless steel connector below has an integrated keying and retention mechanism built into the connector housing. Extremely high reliability applications may use metal sheathing along the cable rather than rubber. This is the maximally rugged option you’ll find on the market and it will be strong enough to withstand crushing forces during operation.
Together with the corrosion resistance of stainless steel, these connectors are an excellent option in many application areas where long-term exposure to moisture or noxious substances creates a risk of system failure.

Hygienic Applications
While not a necessity for every application or environment, some stainless steels can inhibit bacterial growth. These connector materials are formed either by modifying the bulk composition of the alloy, or by applying an antimicrobial film to the surface.
Medical equipment and food service equipment are two areas where this is important, as well as in some sterile industrial environments. Stainless steel connectors that are waterproofed are also valuable in these applications as they will frequently be exposed to liquids, including corrosive sterilization solutions that could damage other connector materials.
Marine Applications
Marine environments are unique in that vessels require everything have rugged construction as well as corrosion resistance. In addition, electrical connector housings for use in marine environments should be sealed against the elements so that the connector meets IP67/IP68 requirements.
316 stainless alloys are ideal for these environments due to their higher molybdenum content. Additional nickel and chromium in 316 stainless steels provides added protection against corrosion from salt water, as well as a self-healing chromium oxide film that resists micro-cracks and pitting on exposed surfaces.
The same benefits of 316 stainless steels apply more generally in rugged industrial applications where corrosion resistance is a risk. Corrosive substances are pervasive in industrial systems, including exposure to chlorine-containing compounds and salts that may corrode materials like brass. Stainless steel connectors provide the corrosion resistance needed to ensure maximum reliability in these applications.
Our VULCON STEEL line has a salt spray tested rating in excess of 96 hours to ensure reliable performance in marine environments.
Custom Stainless Steel Connector Options
While many standard connector and interconnect styles are available in stainless steel housings, some systems will require a custom connector and cable assembly to fulfill operational requirements.
In cases where an existing system needs to be retrofitted with a more reliable connector option to ensure long-term reliability, a custom connector is a cost-effective approach to extending a system’s lifetime. Similarly, if considered early-on in system design, a custom connector allows a designer to be more creative in terms of form factor while still ensuring performance in harsh environments.
Stainless steel fabrication is simple enough that manufacturers can produce custom connectors or adapt existing connectors into new styles where corrosion resistance is required. Engineers that have identified stainless steel as an ideal corrosion-resistive connector material should consult a manufacturer regarding custom connector options. Some custom housing options include Circular Connector housings and modular versions of standard connectors and cable assemblies.
When you need rugged connectors and custom stainless steel electrical connectors that can operate reliably in harsh environments, including where exposure to corrosive substances may occur, look to Norcomp for standardized or customizable interconnect solutions.
Norcomp’s product lines are Rugged Environment Certified (REC) and are ideal for use in robotics, military, industrial equipment, marine, and other demanding applications. Contact Norcomp today to learn more about our standard ro custom interconnect solutions.
Need a custom stainless-steel connector solution to finish your design?
Custom Stainless-Steel Connector Solutions
Go Back