Products
- Circular Connectors & Cable Assemblies
- D-Sub Connectors
- IP67 D-Sub Connectors
- D-Sub Backshells
- Micro-D Connectors & Cable Assemblies
- Power-D & Combo Mixed Connectors
- Push Pull Connectors
- D-Sub & Micro D Hardware
- Modular RJ45 Connectors
- USB Connectors
- D-Sub Adapters & Gender Changers
- SCSI .085"/.050"
- .050 Ribbon
- Headers & Receptacles
- Bayonet Connectors
Why You Should Consider Connectors Early in the Design Process
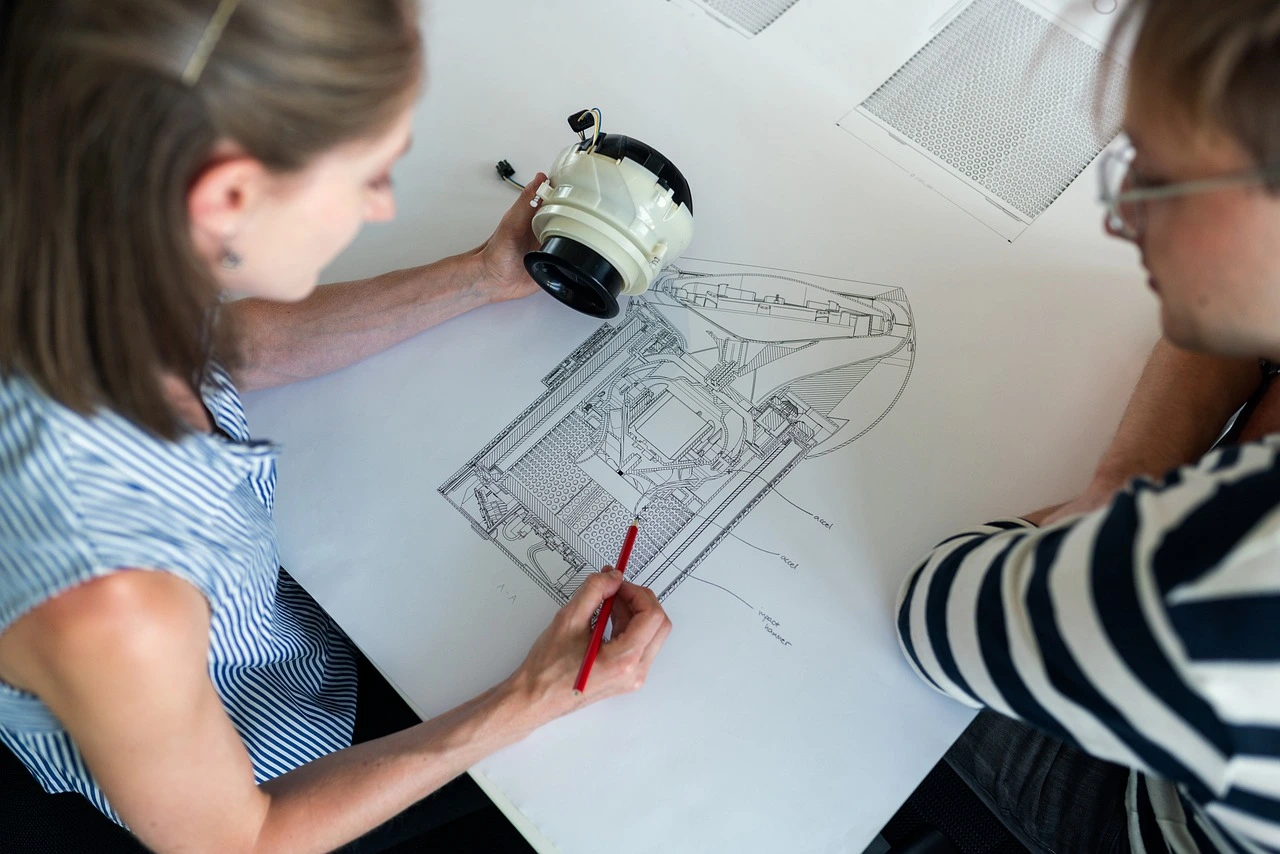
Complex highly-integrated systems rely on connectors to route power and signals between different boards, modules, and components. Based on the application, as well as the form factor and mechanical characteristics, connectors can become a design challenge. However, the right connector can be an enabler of innovation by providing highly reliable, low-loss connections for data and power. That’s why connectors play such a key role in advanced electronics from robotics to industrial controls, telematics and more.
Since connectors are so important across applications, they should be selected early on in the design process rather than waiting until board and enclosure designs are finished. If a designer waits until the end of a design to select connectors, there are some risks involved that could trigger a redesign, either in terms of the electronics, mechanical design, or both. Considering connectors as a primary element that drives the physical design of your system avoids the risk of a redesign.
What Are the Risks of Delaying Connector Selection?
There are many aspects to consider when selecting components for an electronic system, including connectors. Unlike semiconductors or other electronic components, connector selection relies as much on mechanical requirements as it does on electrical performance.
Thorough consideration of both mechanical and electrical constraints helps to avoid problems in the following areas:
Mechanical Interference
Arguably the most common challenge arising from late selection of connectors is mechanical interference within the device enclosure. Mechanical interference can occur with other components on a PCB, components outside the enclosure, or with the enclosure itself.
Instead of selecting connectors to fit inside a pre-existing enclosure, the enclosure can be designed to accommodate the connector. This is the standard approach to mating enclosures and connectors by mechanical designers, particularly when using standard form factors like circular connectors, d-sub connectors, or rectangular connectors.
Operating Environment Mismatch
If you’ve finished the physical system design and layout and are left with a limited range of connector options, it’s possible the connector does not meet the basic reliability or operating requirements. Certain connectors that are constrained by form factor might not meet operating requirements, such as:
- Power handling requirements
- Mechanical shock or vibration
- Resistance to moisture ingress or other contaminants (dust, chemicals, etc.)
- Cycling to extreme temperatures or thermal shock
Addressing connector design early on is the best approach to ensure environmental risks are accounted for in the finished product. Some connector manufacturers offer high-reliability connectors that specifically target the points listed above; these are available in standard form factors and may be Rugged Environment Certified.
If a connector will be used in a harsh environment, make sure to check the manufacturer’s IP rating, which will define it’s protection level against dust and water exposure.
Power, Signal Integrity, and Reliability
Advanced electronic systems are operating at higher speeds, potentially creating signal integrity problems during data transfer. Depending on signal edge rates and data rates, connectors and cables may need to be fully shielded and impedance controlled. This needs to be determined before completing the physical layout for a system.
Standard off-the-shelf connectors for digital data transfer may not be able to withstand deployment in harsh environments, so overmolded connectors might be necessary. These connectors may also create mechanical interference if not selected early in the design process.
Power handling is another important point, and it’s important to consider the voltage/current ratings for a connector alongside reliability and form factor. Physically smaller connectors may have limited power handling capability, making them unsuitable for certain applications.
Other important aspects like insulation materials and geometry of available connectors will dictate the voltage rating. These electrical parameters will drive the required form factor for the connector, which then should drive the mechanical design of the system.
Improper Termination
Connector termination defines how a connector is attached to individual conductors, whether discrete wires or jacketed cable. The termination style used in a connector may affect the connector’s ability to be sealed against the external environment, as well as its mechanical strength. Termination method can also impact assembly and manufacturability, and the final decision on contact type should be made after a thorough DFM review and discussion with the manufacturer or assembler.
If waiting until a design is finished to select connectors, the available connectors may not provide the termination style needed to ensure high reliability. When available space is limited, certain connectors may not fit in the design, or they may be costly to assemble. Just as is the case in other aspects of electronics design, a thorough DFM review early in the design process can help a design team select the best connectors for their application.
Select Connectors Early and Avoid Redesigns
A problem in any of the above areas could trigger a costly redesign, and the extent of any required redesign could vary widely. This could be as simple as moving an opening in the device enclosure, or it could require extensive redesigns of system components, including circuit boards and cable assemblies. The risks involved are clearly significant, but they can be eliminated by looking at mechanical aspects of your system early.
Because connectors are such a major determinant of reliability, it’s best to approach connector design and selection at the beginning of system design. In some cases, you may be constrained to a standardized form factor, and this constraint should drive the system’s mechanical and electrical design. When there’s some freedom to select a connector, a decision to use a standard or custom connector/cable assembly should be made early.
When you need rugged connectors for robot design and engineering that can withstand deployment in harsh environments, look to NorComp for standardized or customizable interconnect solutions. NorComp's product lines are Rugged Environment Certified (REC) and are ideal for use in robotics, military, industrial equipment, and other demanding applications. Contact NorComp today to learn more about our standard or custom interconnect solutions.
Sometimes you can't afford to redesign for any existing connectors and need a custom solution to finish your design.
Go Back