Products
- Circular Connectors & Cable Assemblies
- D-Sub Connectors
- IP67 D-Sub Connectors
- D-Sub Backshells
- Micro-D Connectors & Cable Assemblies
- Power-D & Combo Mixed Connectors
- Push Pull Connectors
- D-Sub & Micro D Hardware
- Modular RJ45 Connectors
- USB Connectors
- D-Sub Adapters & Gender Changers
- SCSI .085"/.050"
- .050 Ribbon
- Headers & Receptacles
- Bayonet Connectors
DESIGNING DELIVERY DRONES FOR ENVIRONMENTAL SURVIVABILITY
What Happened to Delivery Drones?
Critical Design Considerations for Widespread Adoption
There are many significant factors to consider in autonomous robotics design, but for outdoor applications, environmental survivability is one of the most important.
One of the most buzzworthy aspects of the current robotics landscape is recent advancements in battery and sensor performance that are driving mobility in the delivery space (Figure 1). The flexible and scalable aspects of automation in the supply chain is an important force-multiplier in business and will change how people do business worldwide.
This is especially significant when it comes to the growth in “last mile” delivery drones, intended for the last step in the delivery process – the final link in the supply chain between origin and destination.
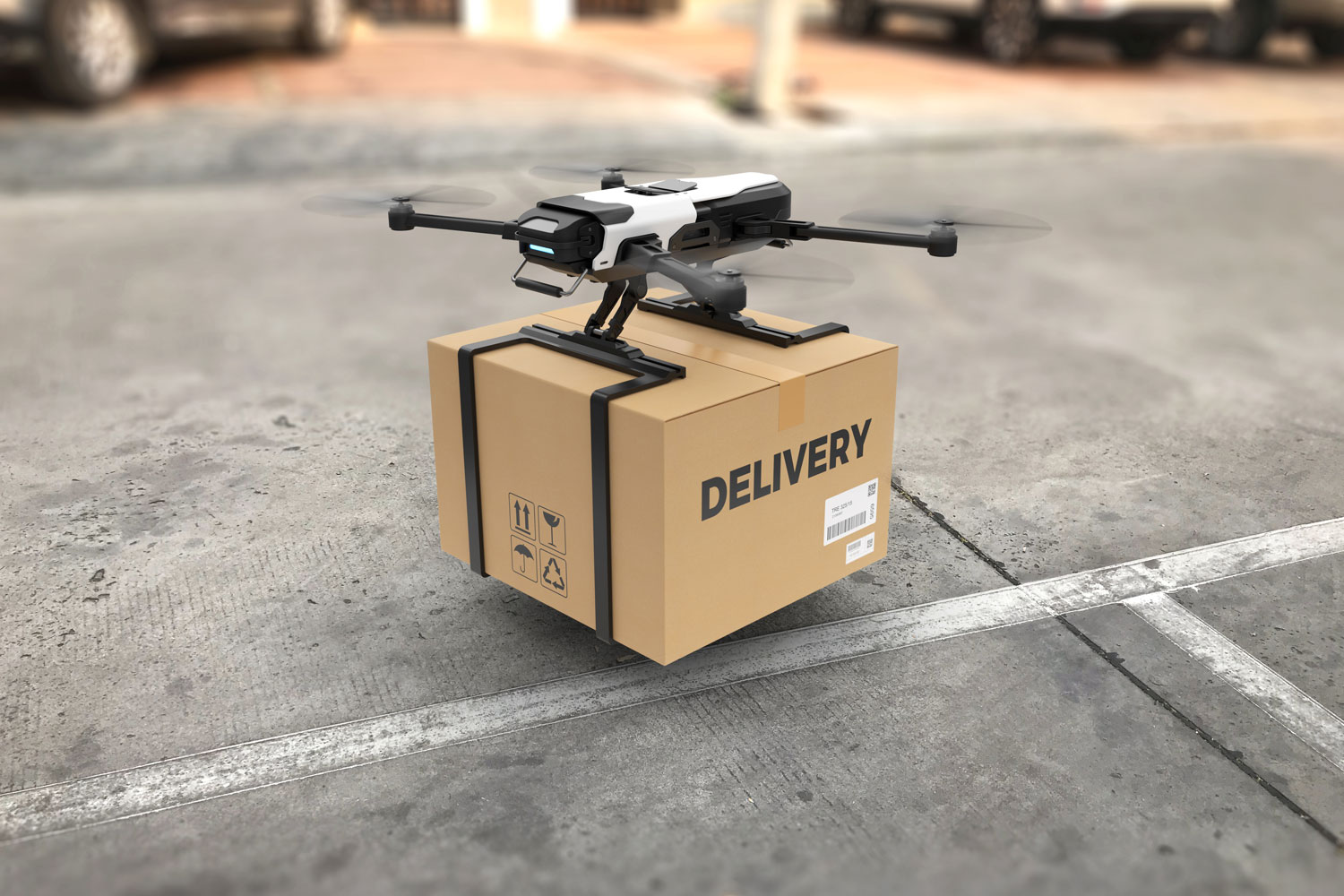
Figure 1: The electrification of unmanned mobility in the delivery space is significant.
There are a plethora of issues surrounding the design of delivery drones including power management and sensor integration, but if the environmental survivability of the entire system isn’t completely addressed, the unit is very likely to fail. Failure modes can range from water and moisture damage and physical shock to vermin and tampering, and must be mitigated to protect the vehicle and ensure reliable operation.
Weatherproofing: How to Protect Delivery Drones from Water, Dust, and Moisture
The first level of environmental protection involves sealing all sensitive areas of the vehicle to a water-tight level of protection. This is important because water and moisture are extremely damaging to both the electronics driving the vehicle, and the cargo it carries (Figure 2). It is important to note the difference between moisture and water, because a seal that is resistant to moist air but allows wind driven rain to enter is not an adequate solution.
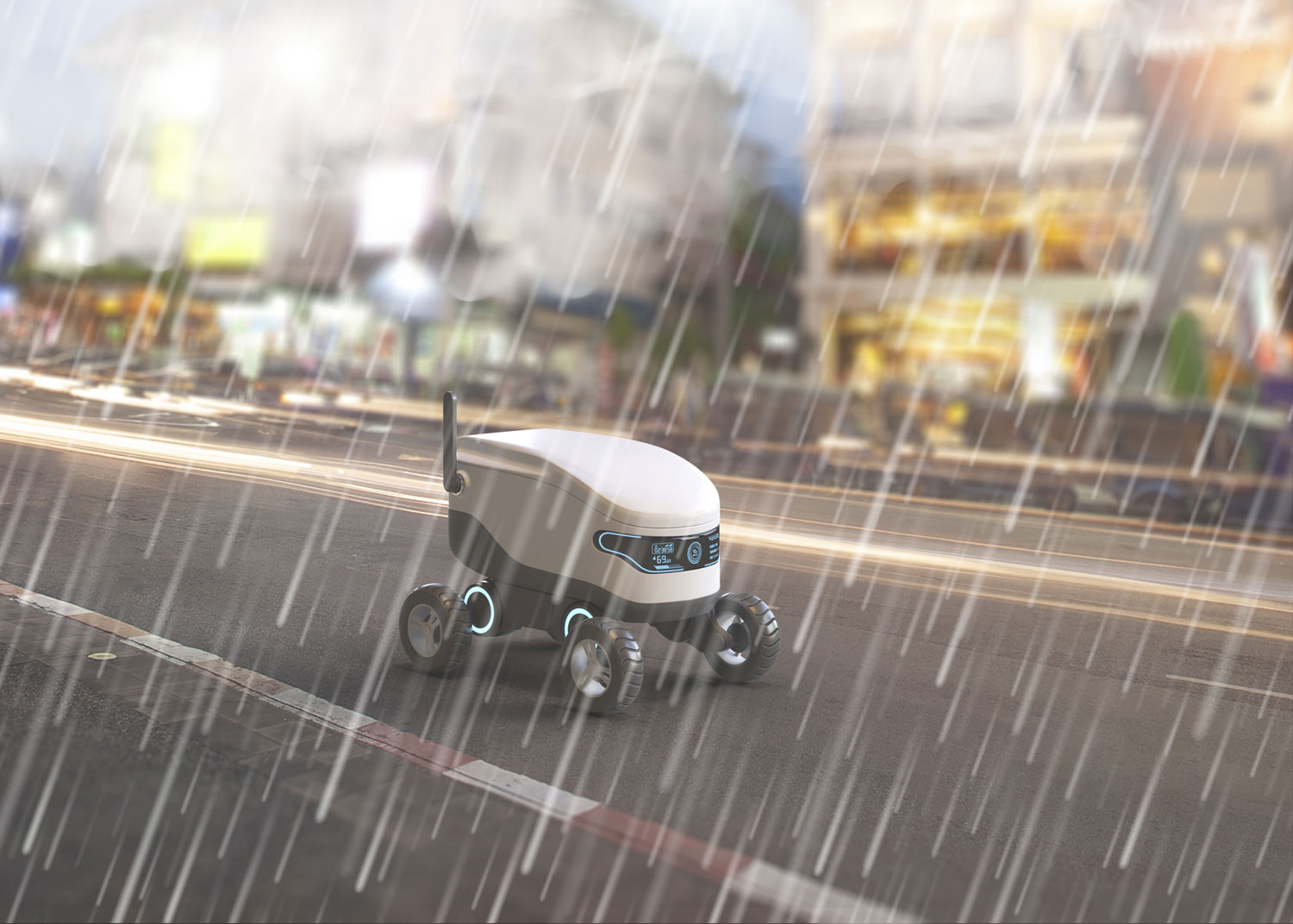
Figure 2: Vehicles operating outdoors must count on water exposure.
Dust, dirt, and particulates are also dangerous to delivery drone systems, for several reasons. Dust and dirt are first and foremost fouling risks, which can clog and damage vehicle systems and contaminate cargo. In addition, many types of dusts and particulates are both conductive and flammable, providing both a short-circuit risk as well as a potential for fire.
The electronics industry generally uses the IEC standard for Ingress Protection to define the level of environmental protection required. This standard uses a two-digit designator - the first digit represents protection against fine solids and tiny particles like dust and sand, ranging from 0, meaning no protection, to 6, meaning full protection. The second digit represents protection against liquids, and ranges from 0 to 9. IP67 is the most prevalent designation, indicating full protection against solid particles and protection against liquids for at least 30 minutes when submerged in shallow (1 meter) water.
How to Avoid Damage from Shock and Vibration
Another major environmental consideration for delivery robots is physical shock and vibration. Causes can range from impacts with other vehicles or undetected obstacles to poor road conditions. If mechanical risks like these aren’t addressed in the design, the resulting damage to both internal and external components and their requisite connections can accumulate until the vehicle becomes inoperable.
As such, it is not only important to protect the vehicles mechanical and electrical subsystems, but to also use ruggedized connectors and cables with proper sealing and vibration mitigation.
Putting it Together: Building Automated Last Mile Delivery Drones That Last
Luckily, these mitigation techniques, when properly deployed in delivery robots, will leverage one another to increase total system reliability and performance. Board-level potting and sealing protect against foreign objects, while providing a damping material to absorb vibration.
Using ruggedized interconnect systems with both IP rated performance and positive latching mechanisms improve both environmental and shock resistance. Every good solution can be a facet of another solution in the system, all contributing to a drone delivery vehicle capable and reliable enough to address last mile delivery.
Update
As single-use plastics are phased out of all designs these delivery drones package delivery systems will need to be designed for reuse-able packaging components.
Solutions such as eliminating the need for bulky wasteful packaging all together with element sealed delivery of minimally package goods.
NorComp high-mating-cycle components allow for repetitive use to promote sustainability while sacrificing non of the performance and convenience.
Go Back